Why choose Debem
The main application advantages of AODD DEBEM pumps refer to their patented and unique operating system on the market. The Debem pneumatic exchanger has no metal parts inside and therefore not subject to corrosion even when the pumps are working in environments saturated with corrosive vapours. It is an anti-stall system, already originally lubricated so it does not require extra lubrication on the air line, is easy to install and has an average life of more than 50,000,000 cycles. DEBEM technology is unique on the market and patented. Here you can see the patents for the pneumatic exchanger and for the FULLFLOW pump.
Our certifications
Patented stall-prevention coaxial pneumatic exchanger
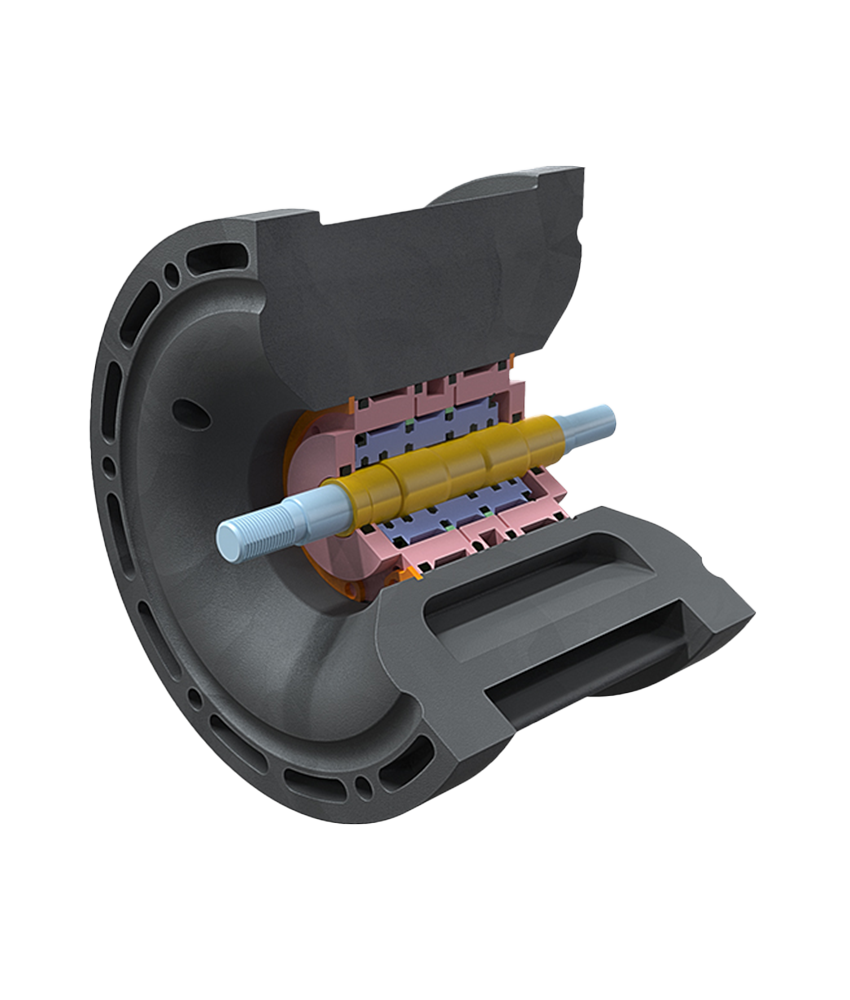
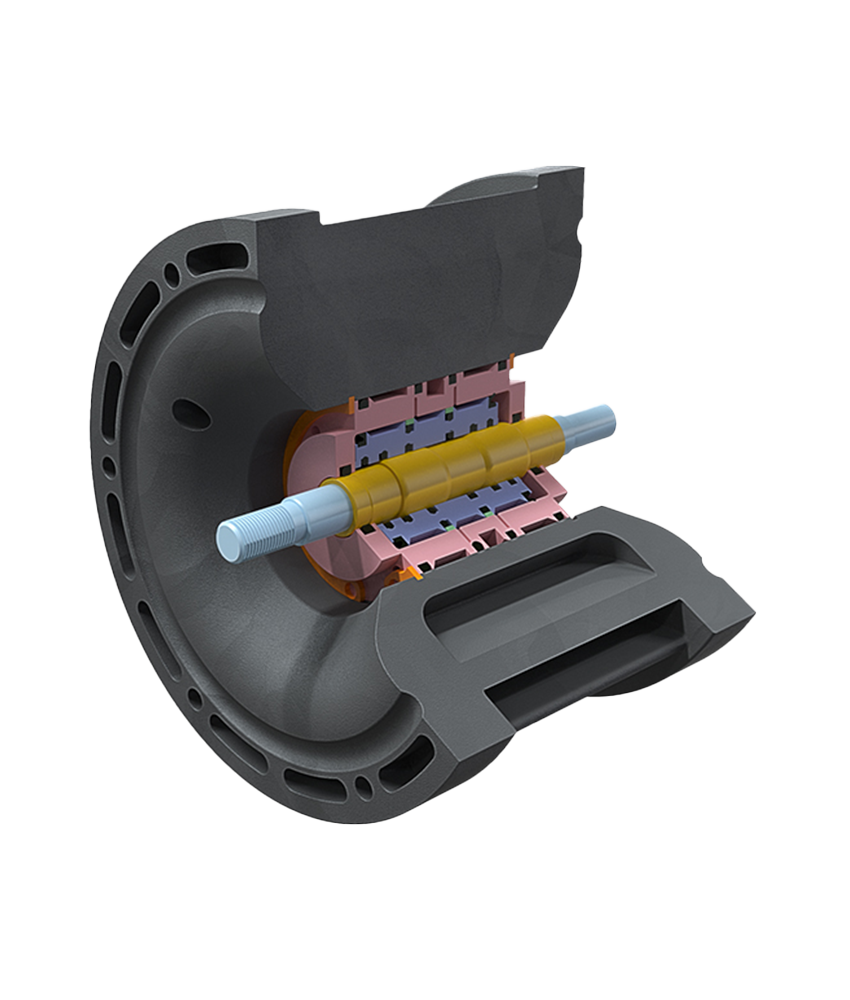
The control part (spool) and the power part (exchanger) are both housed inside the pump in a single block, which limits further losses of load when compressed air flows in the pump. The Debem pneumatic exchanger is easy to repair and/or replace. The internal exchanger is built entirely with plastic parts (except for the shaft connecting the two diaphragms), rendering it resistant to corrosive fluids and fumes. The Debem exchanger is pre-lubricated, therefore the supply air for the pump does not require lubrication, quite the opposite, it must be dried and free of impurities, such as oil, dust or condensation. Debem’s pneumatic exchanger (unique in its kind) is built with an extremely low number of parts, making parts replacement and maintenance extremely easy.
Amongst the lowest air consumptions on the market
Debem’s pumps have been specifically designed to optimise the space on the back of the diaphragms. The volumetric space profiles are developed to guarantee the total dilation of the diaphragms with very small air volumes.
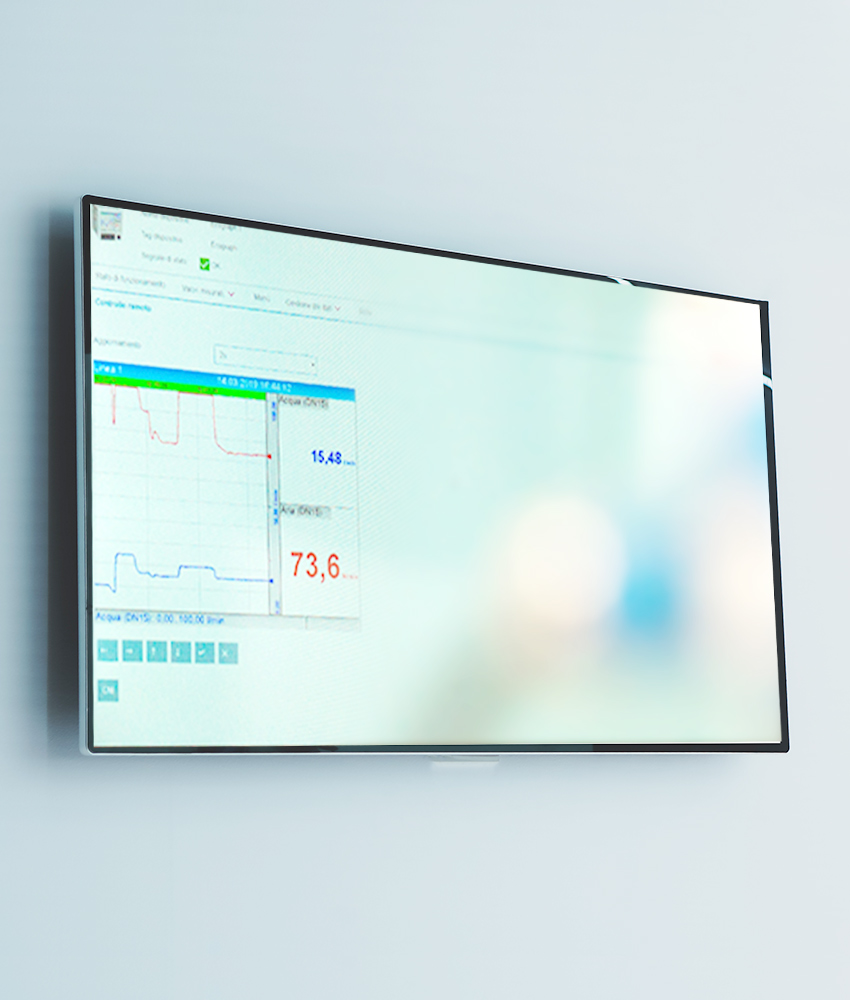
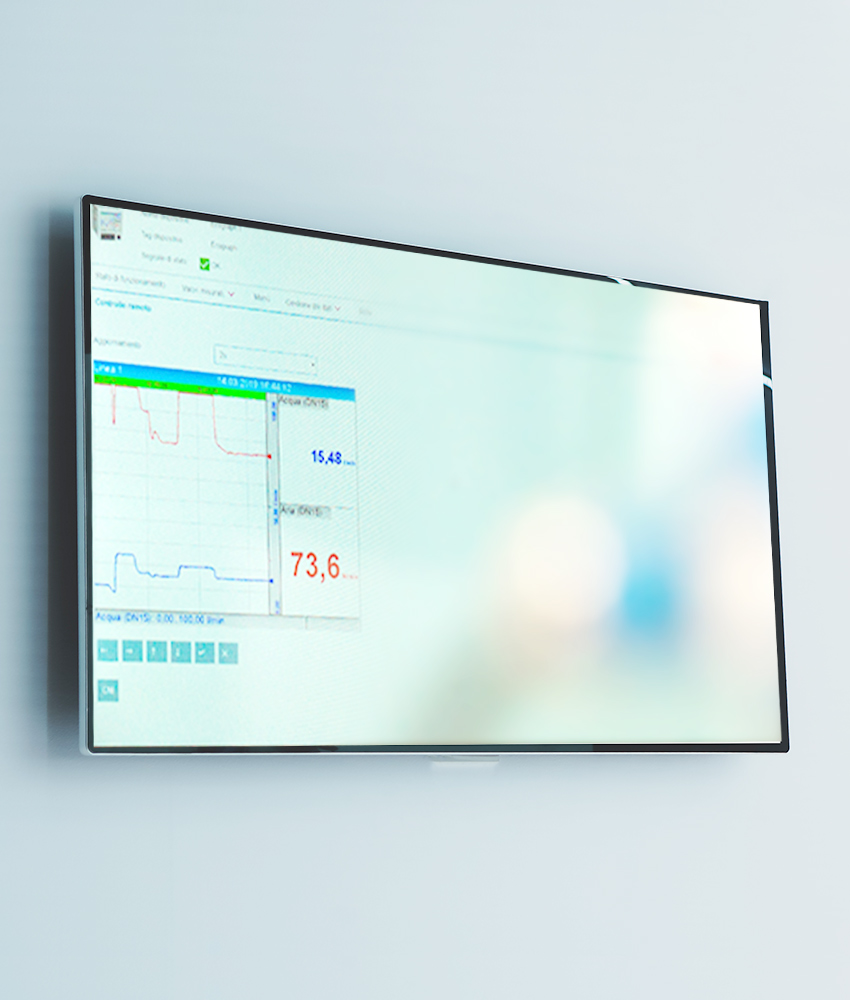
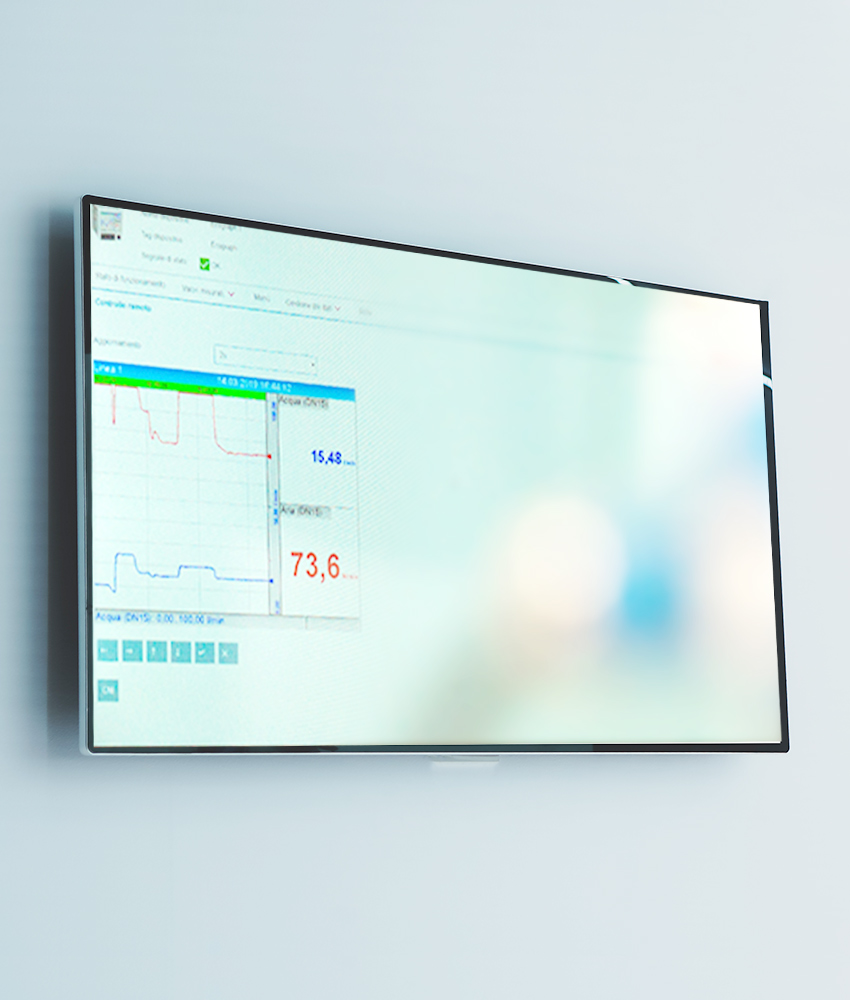
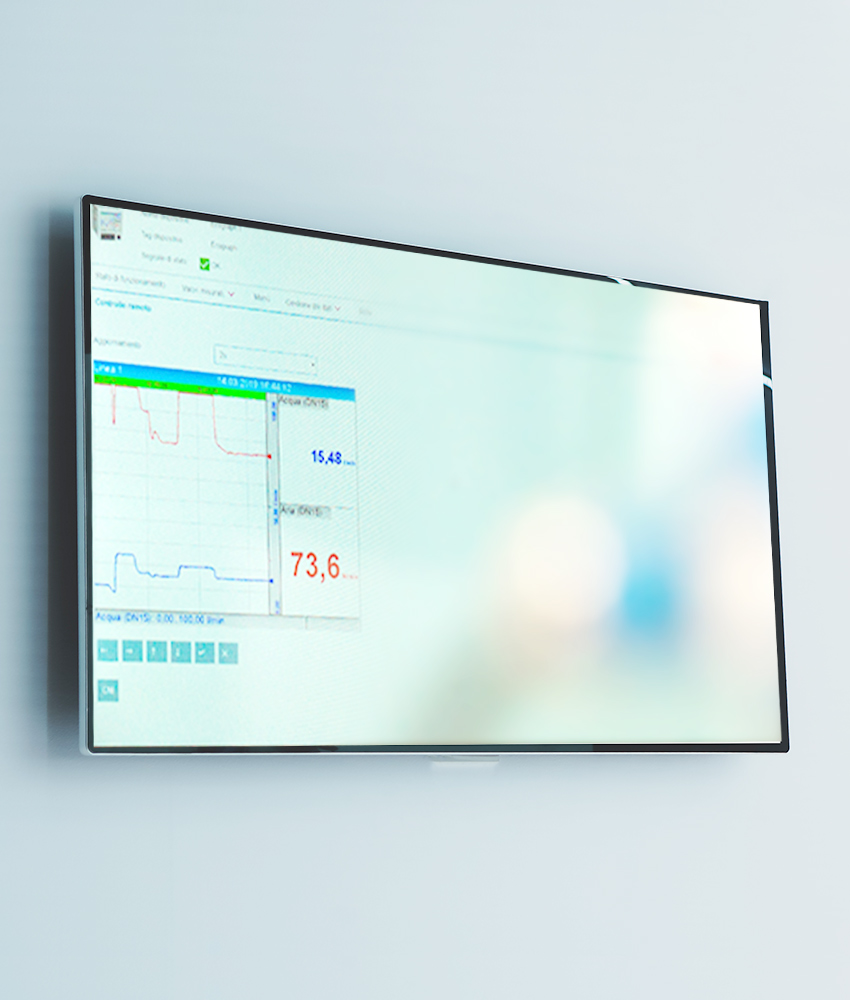
Debem’s pumps are designed to optimise the consumption of air, regardless of whether electronic control systems are used. Our competitors sell this option as an accessory but certain misleading advertising would have you believe that this is a production standard. Be suspicious of all companies that claim technical data without having the instruments necessary to determine their veracity. Debem can count on its own new-concept test bench, with state of the art certified instruments, designed to test and certify the parameters of its own products and the efficiency of the pumps, in compliance with the latest applicable standards and in line with the new European project for INDUSTRIA 4.0.
Flow rates
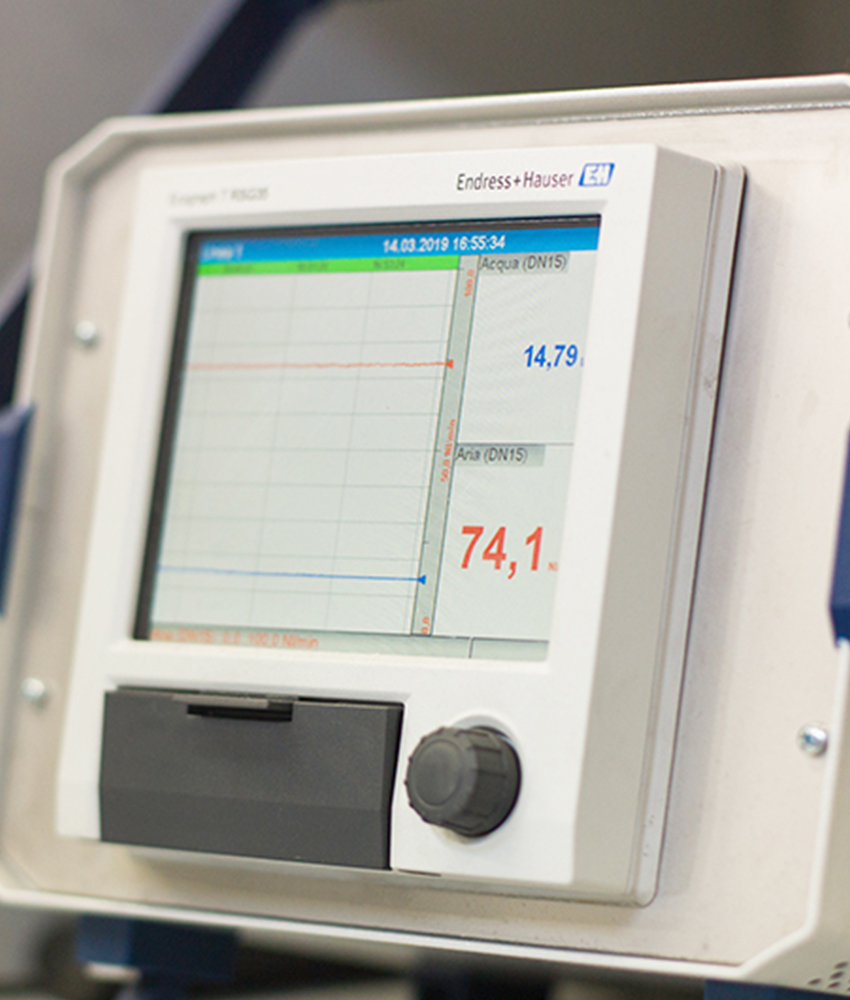
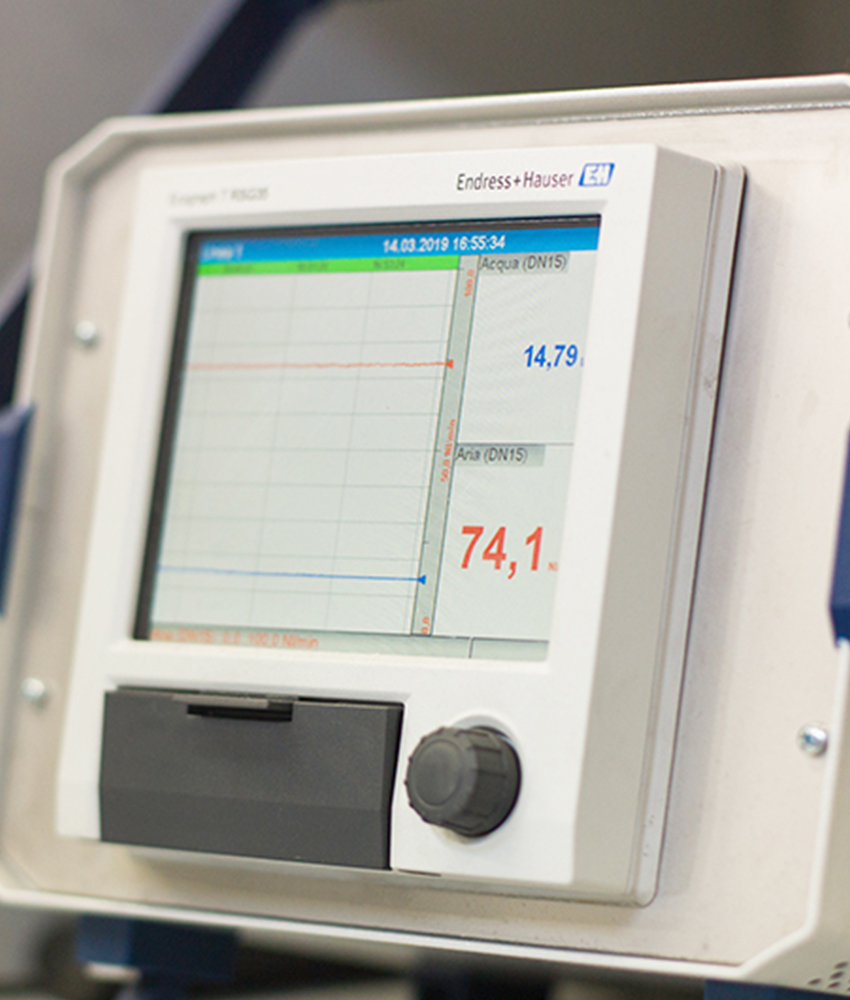
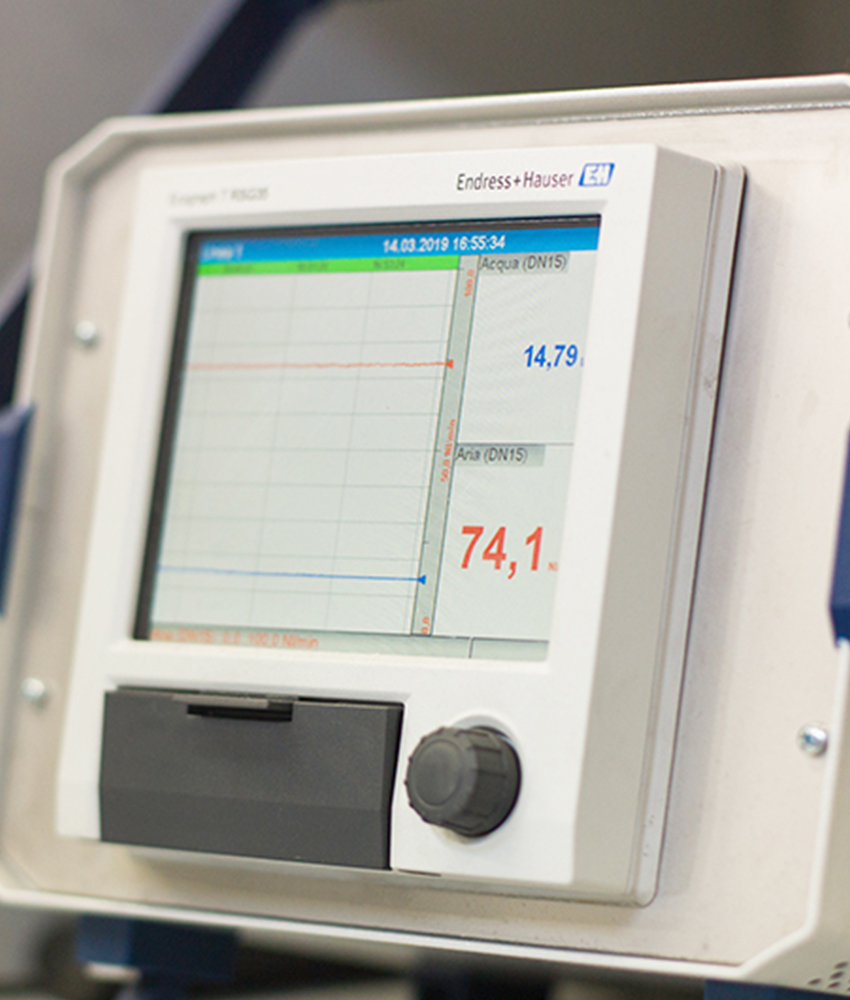
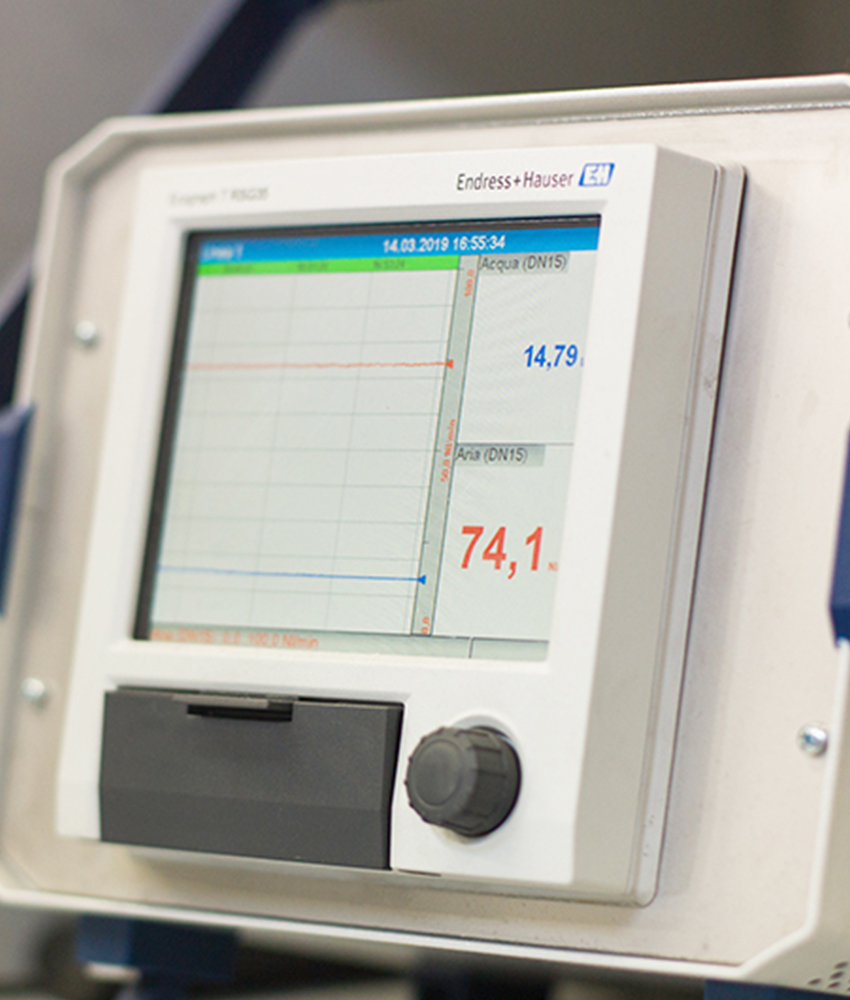
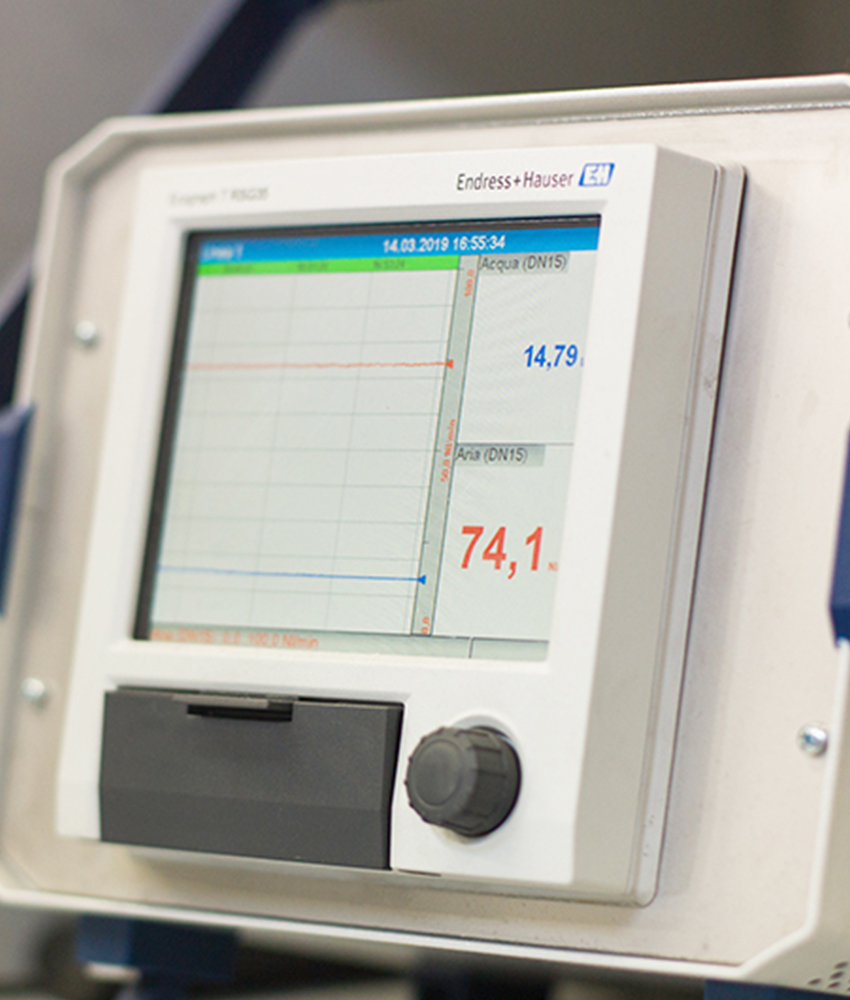
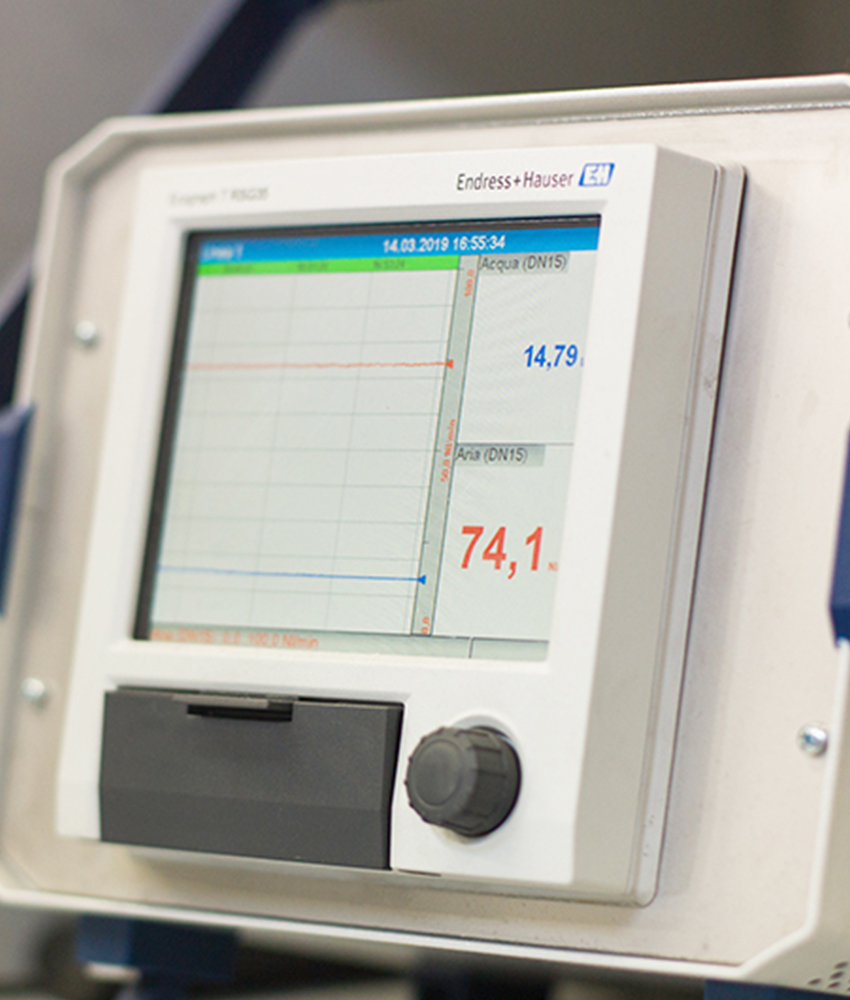
The flow rate that we declare is real. The pumps are tested with a ½ metre of hose in suction. Other companies test them with the suction manifold immersed directly in the fluid, which is why they declare 10/15% more than the actual value.
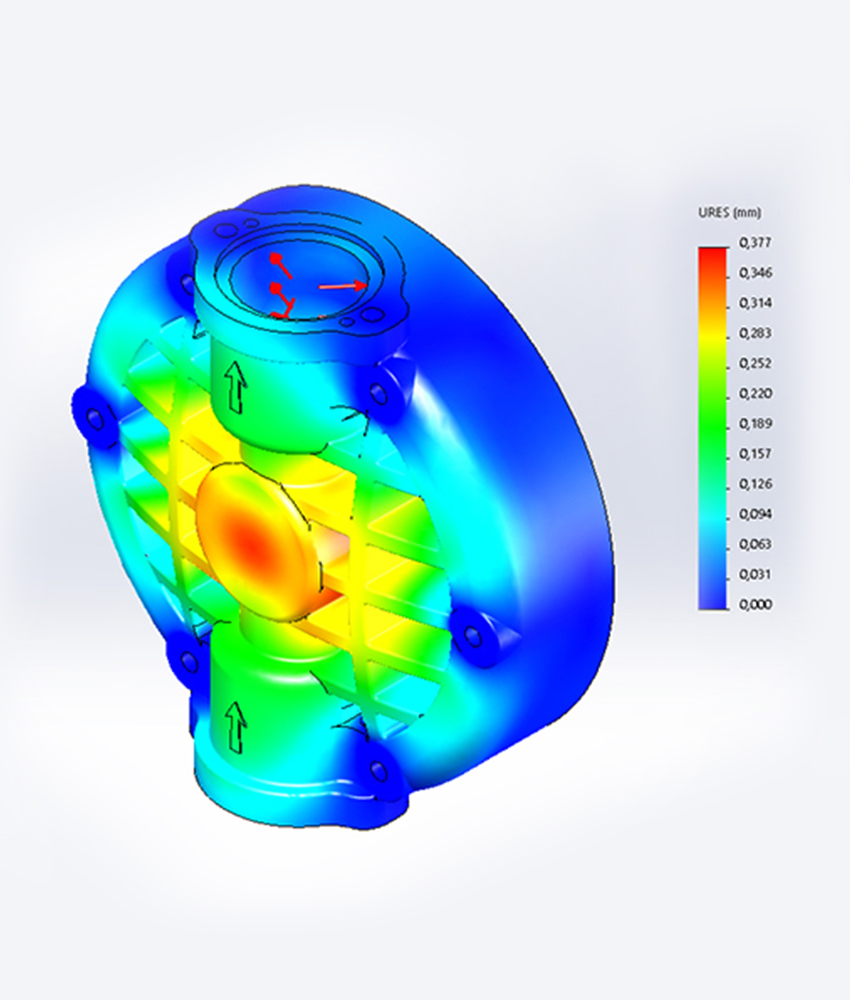
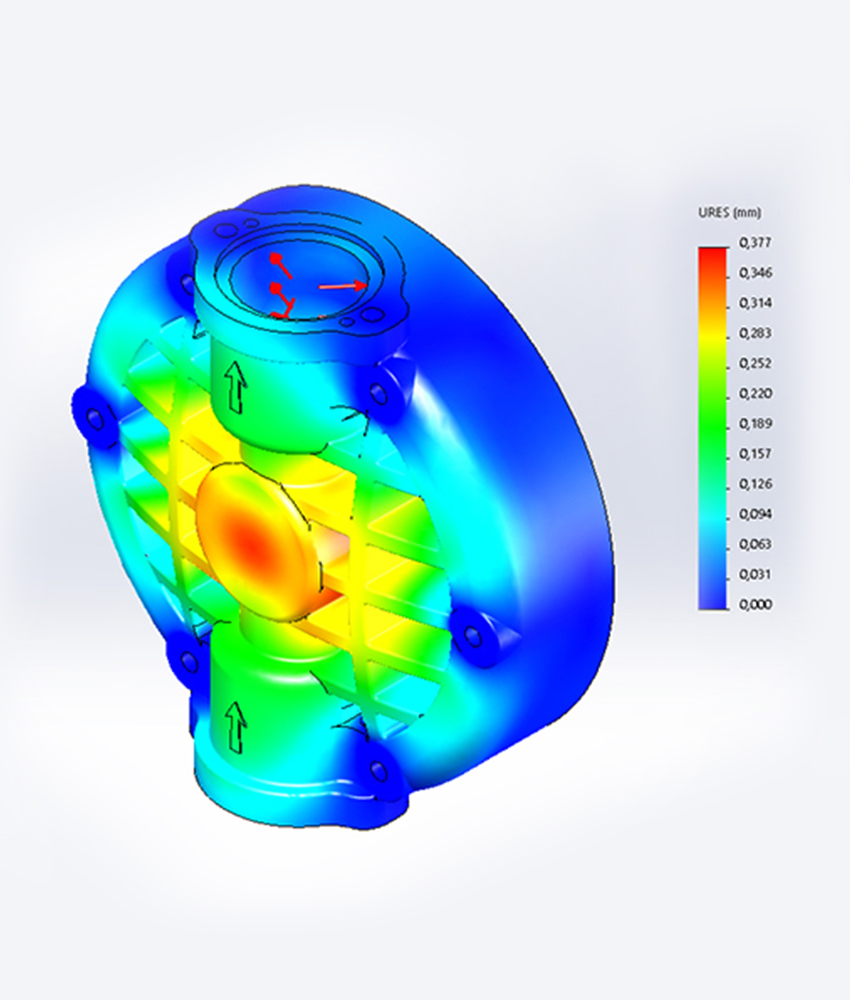
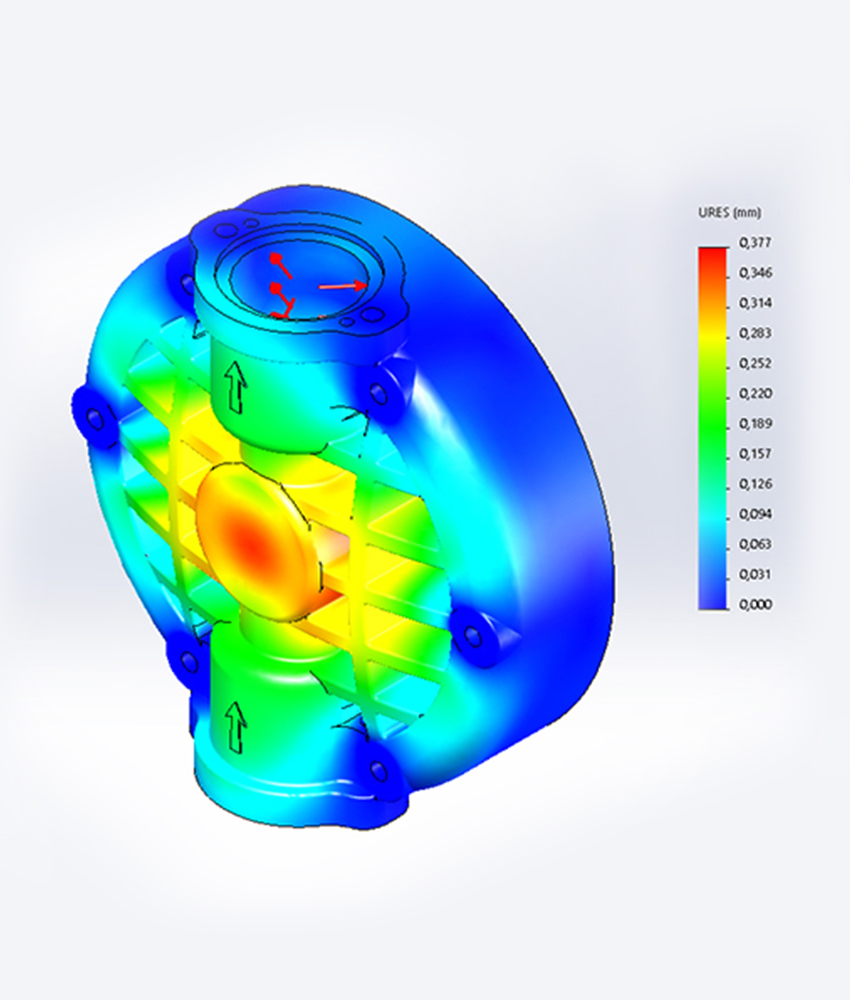
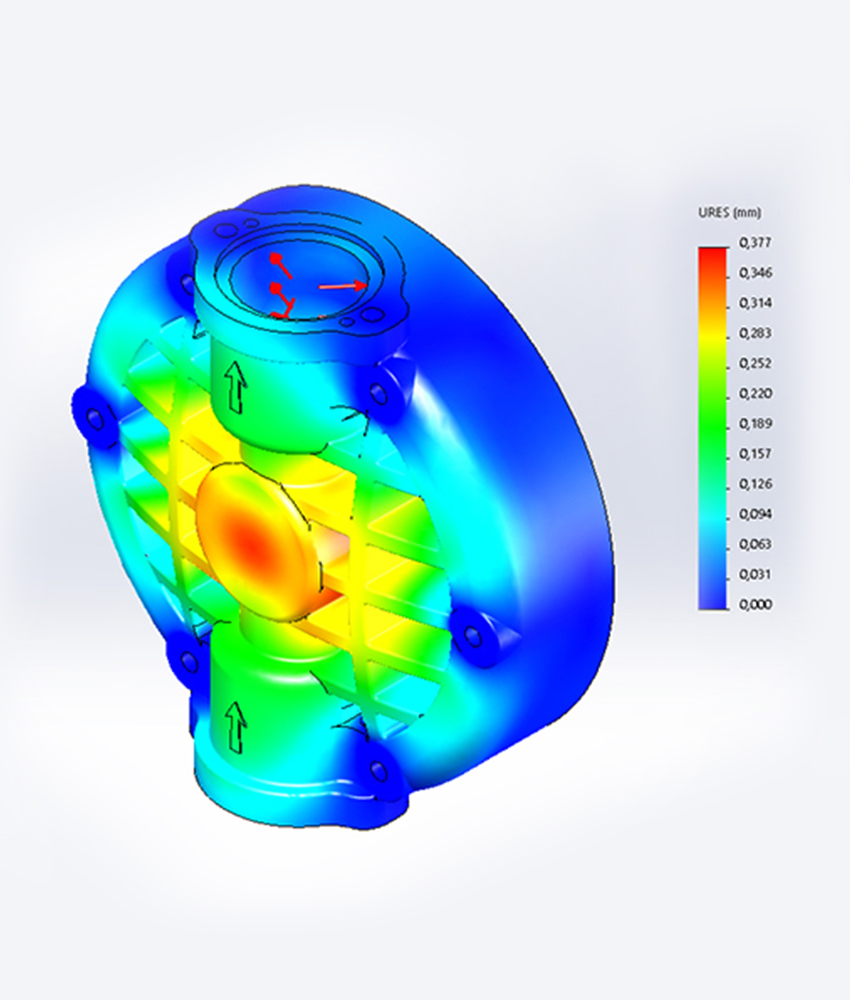
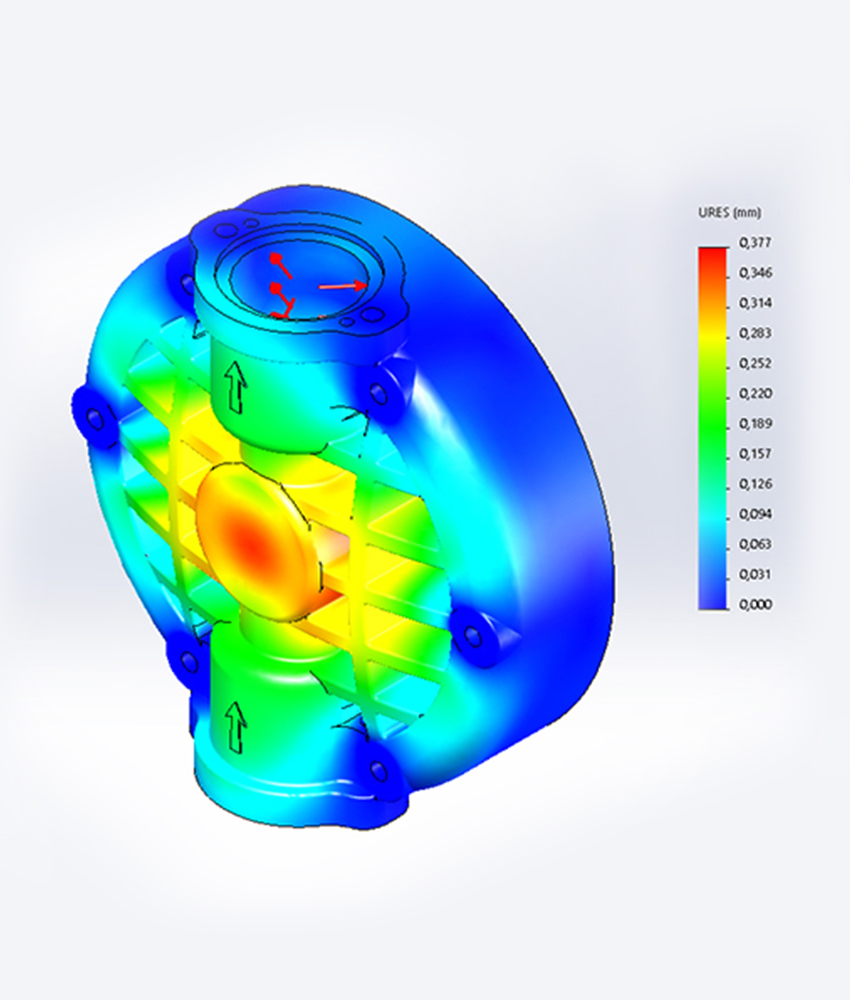
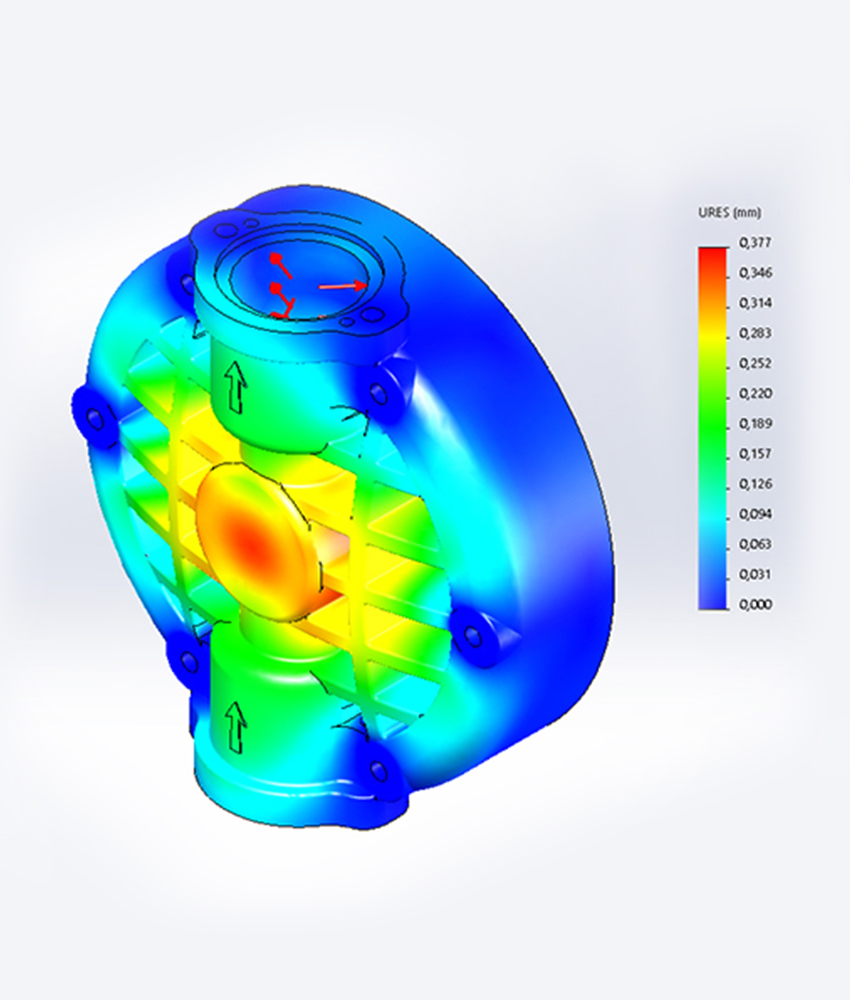
The finite element analysis can be used to predict the risk of failure, speed of wear and correct operation of a product right from the design stage. Even though it is referred to as an analysis, the FEM is an excellent tool to predict the behaviour of a product during its future use.
Diaphragms with LONG-LIFE profile
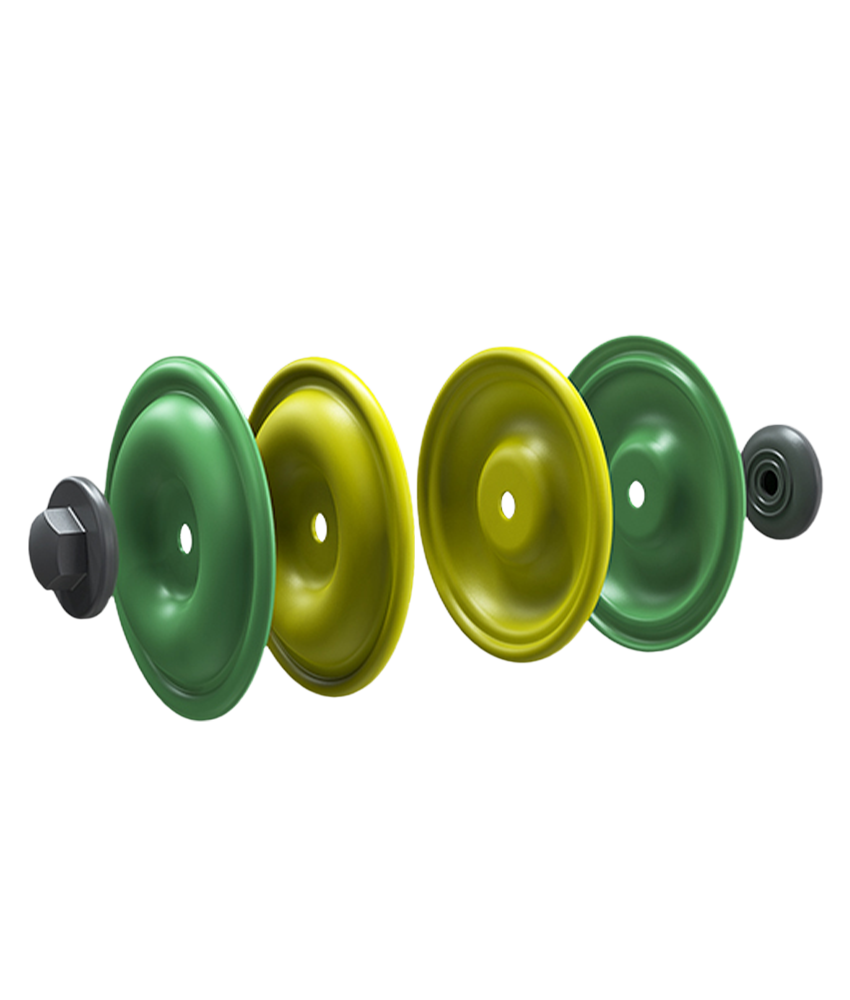
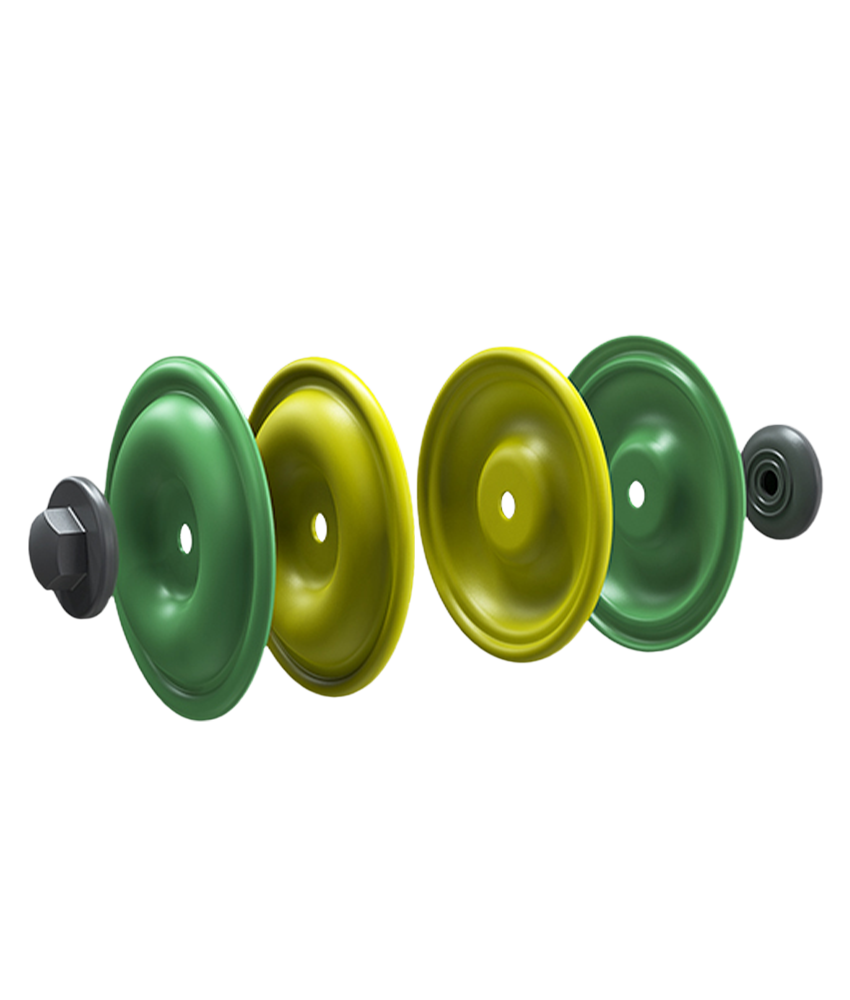
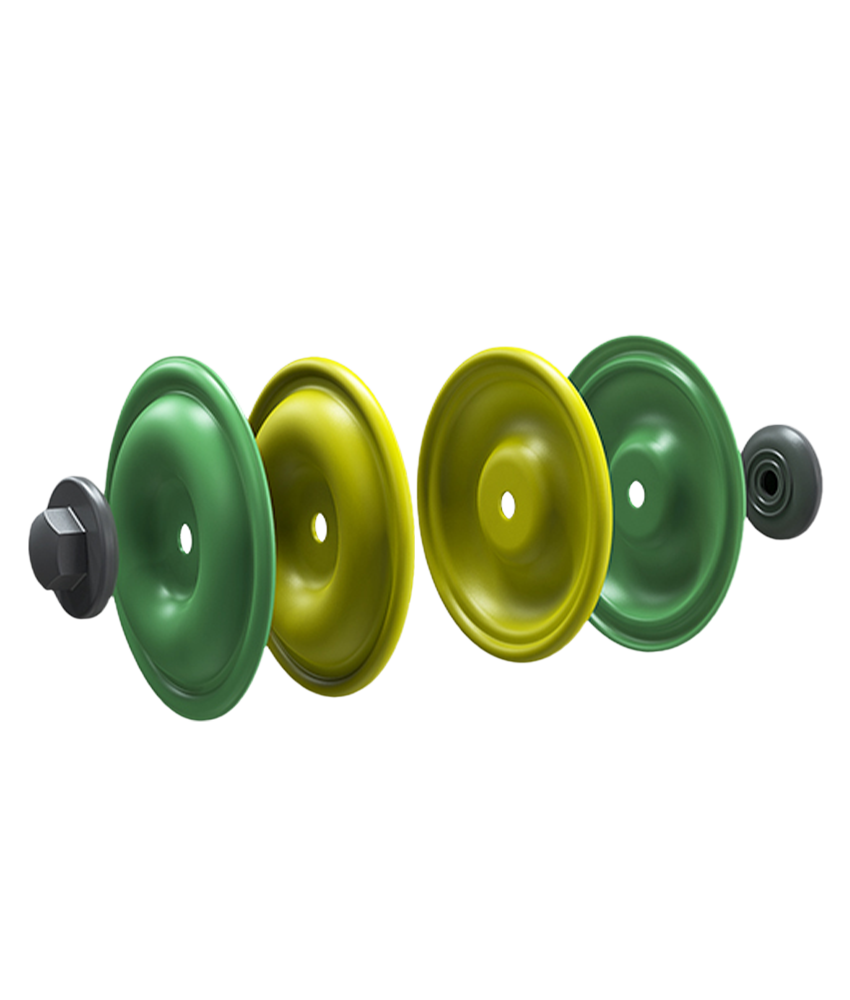
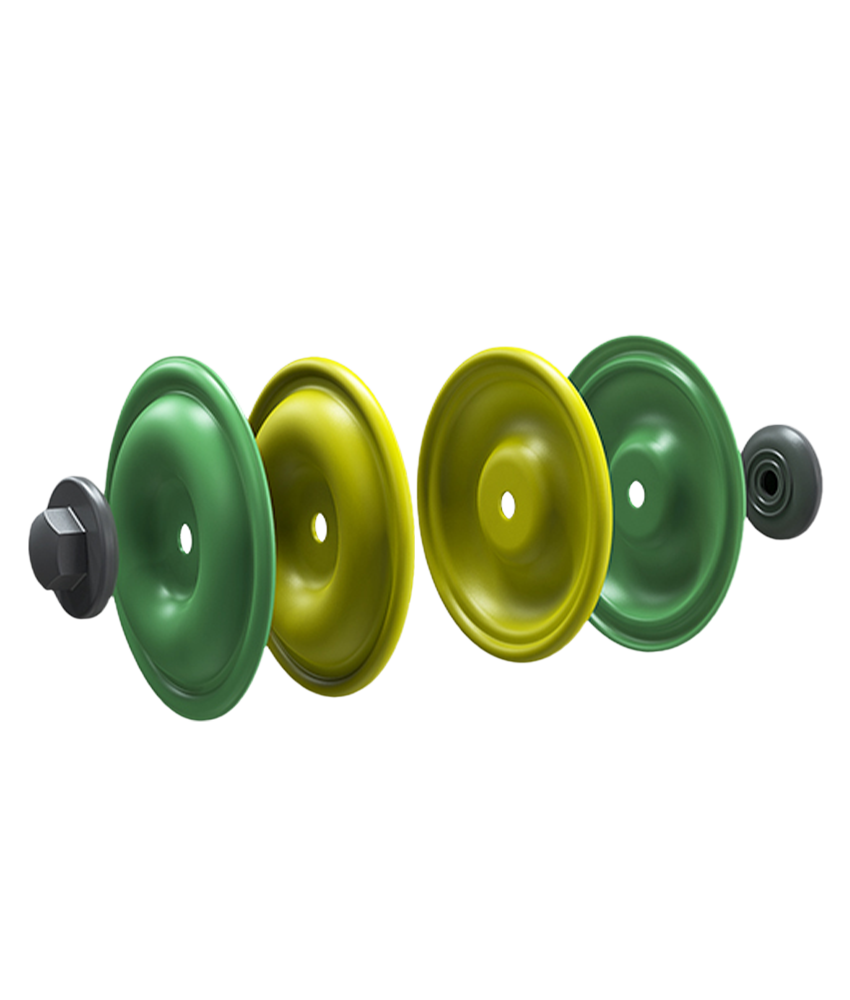
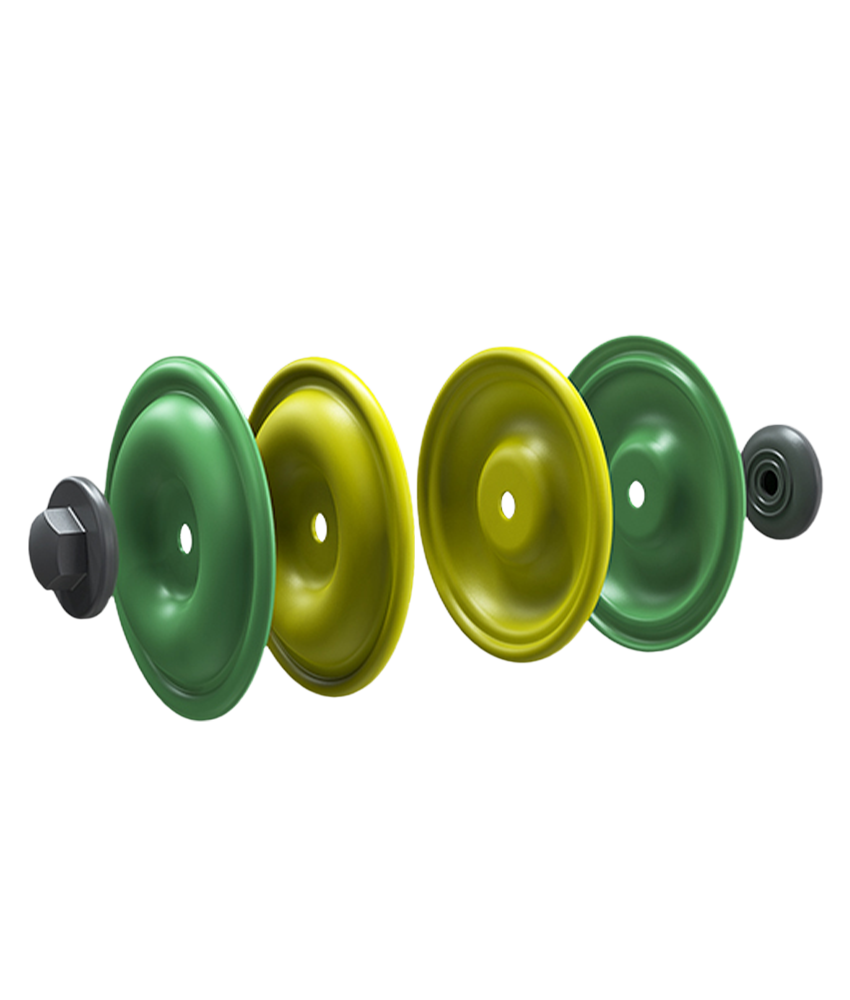
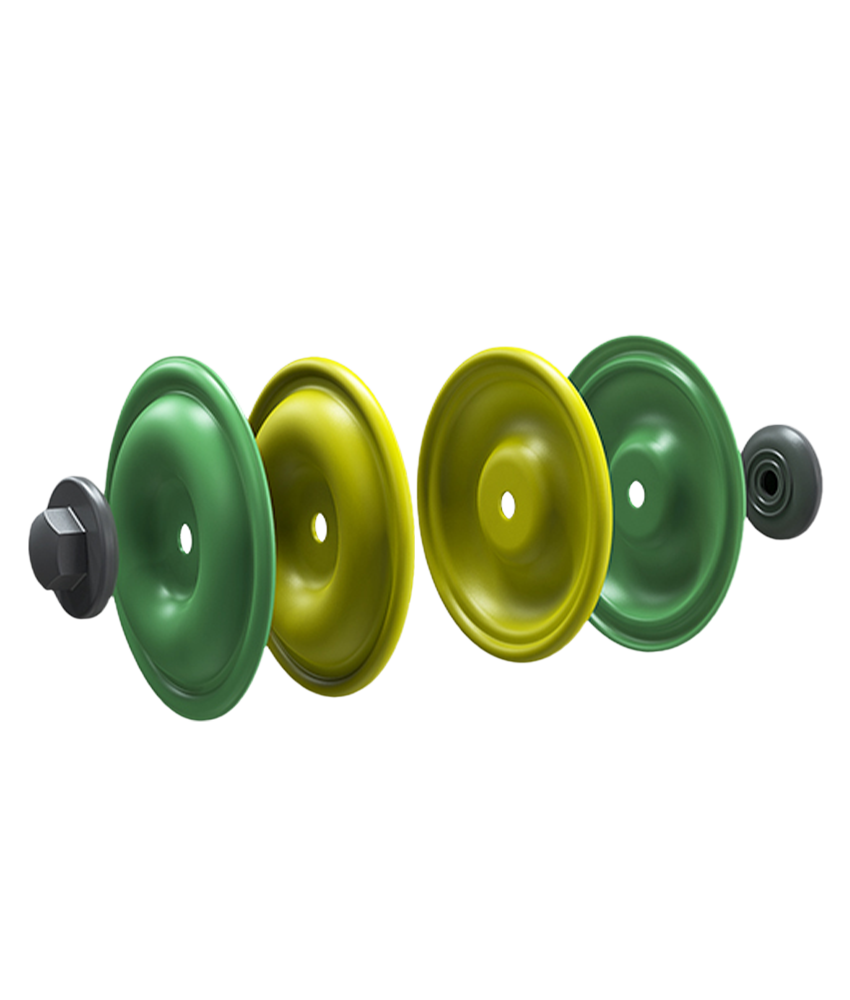
A modern design process, destructing testing, as well as an in-depth analysis of the results have allowed Debem to develop the new generation LONG LIFE diaphragms. Thanks to their profile and construction shape, these products offer a larger working surface and improved redistribution of the load, reducing the stress and yield of the material to a minimum. The profile of our diaphragms is designed so that the mechanical stress (in expansion) is distributed along the whole profile, so that there is one point with the greatest stress. On other diaphragms with a similar design the stress is applied on various points which can compromise the life of the diaphragm. The diaphragms are available in a vast range of materials.
Thermoplastic diaphragms






HYTREL® is a thermoplastic material with unique characteristics such as a high resistance to impact, flex fatigue and creep. At low temperatures it maintains an excellent flexibility under stress and at high temperatures it maintains most of its properties. It is also resistant to the attack of many industrial chemicals, oils, solvents, acid and alkaline fluids, amine and glycol. SANTOPRENE® has an excellent resistance to acid and alkaline fluids, high flexural resistance and good abrasion resistance.
PTFE diaphragms
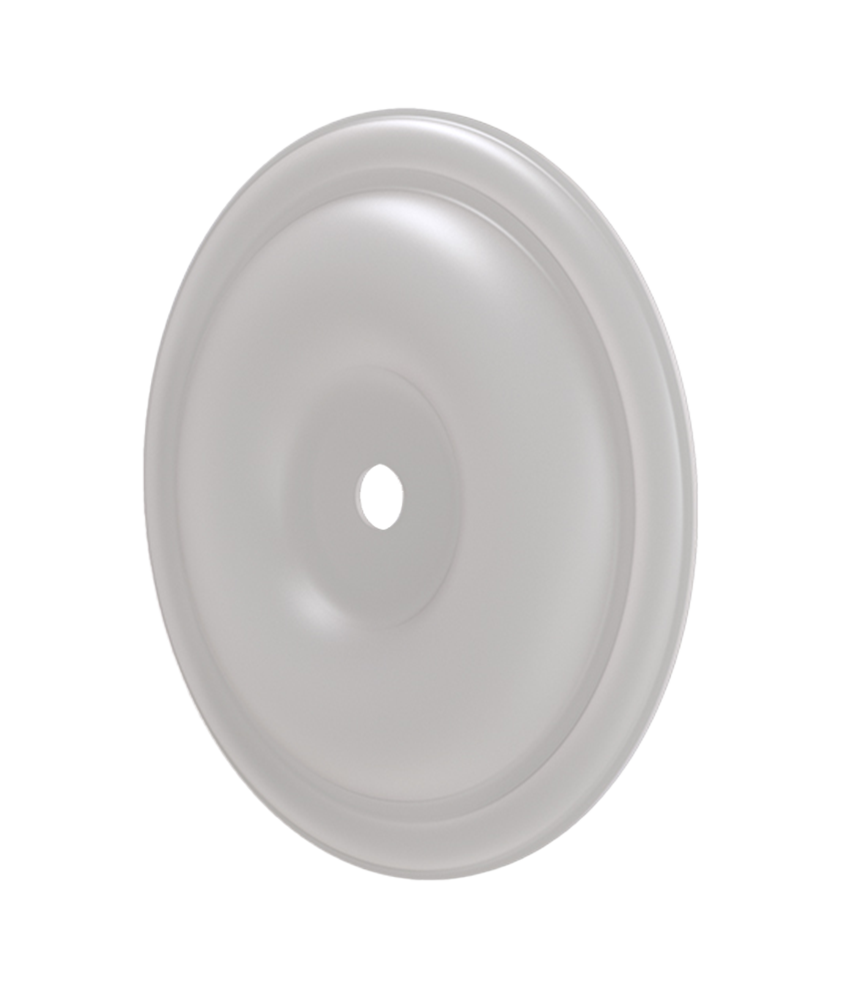
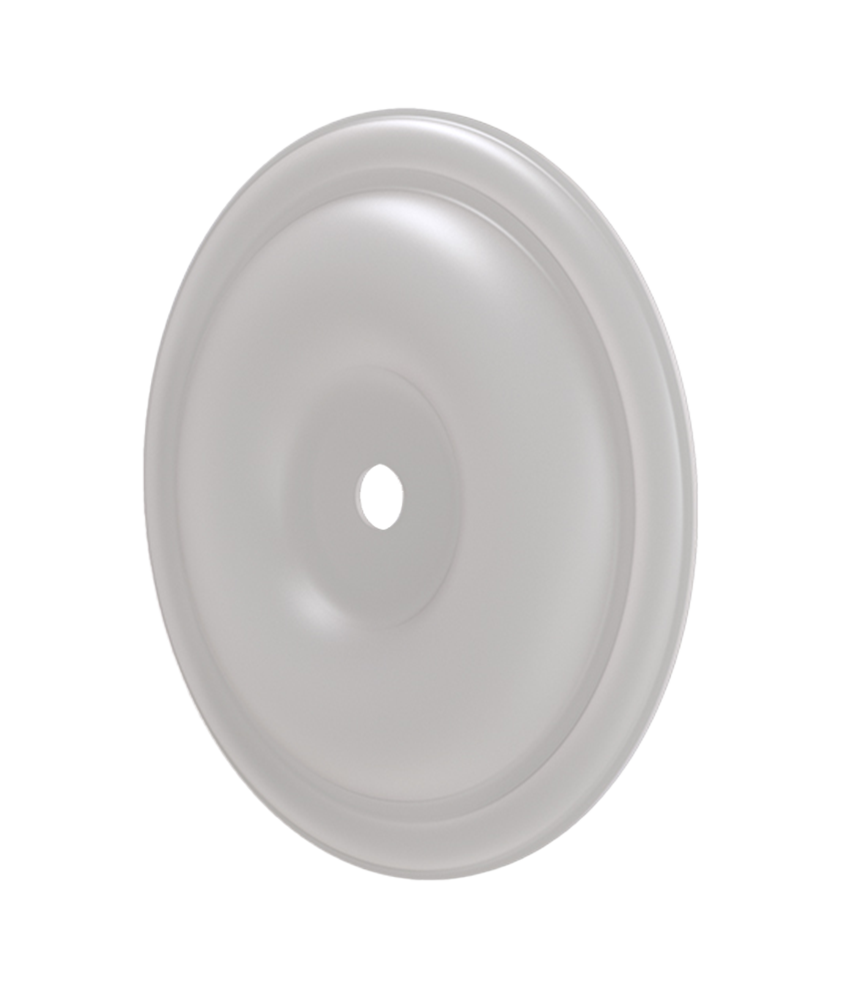
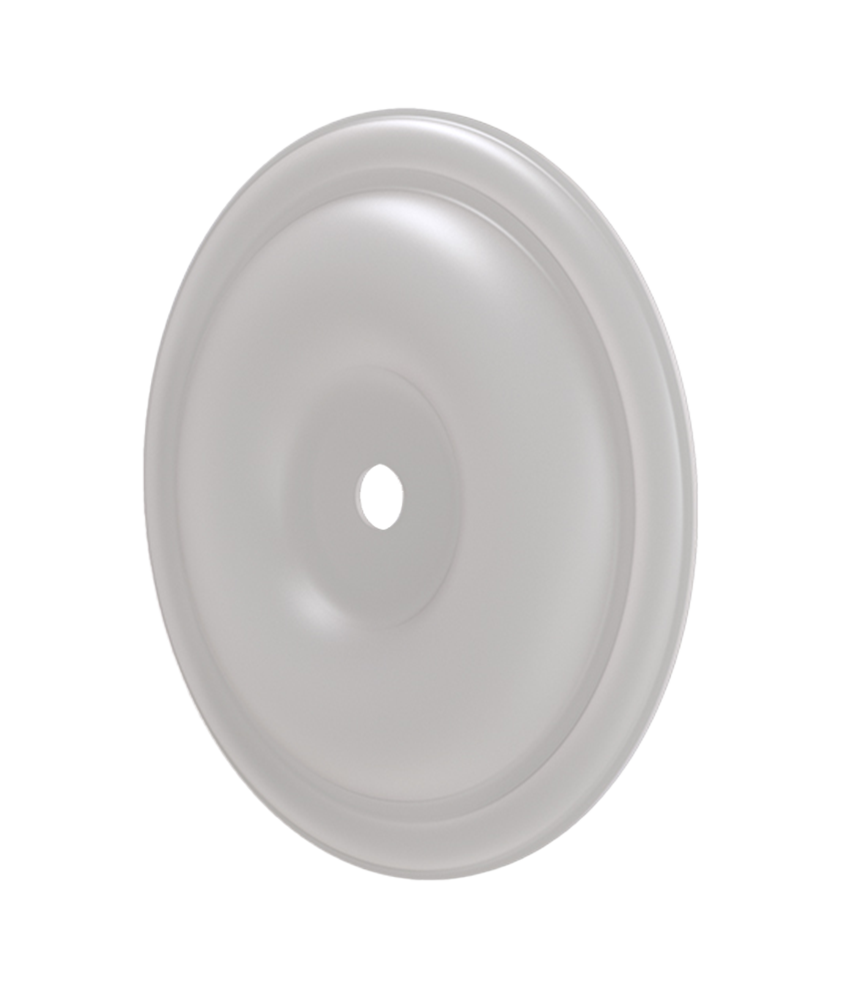
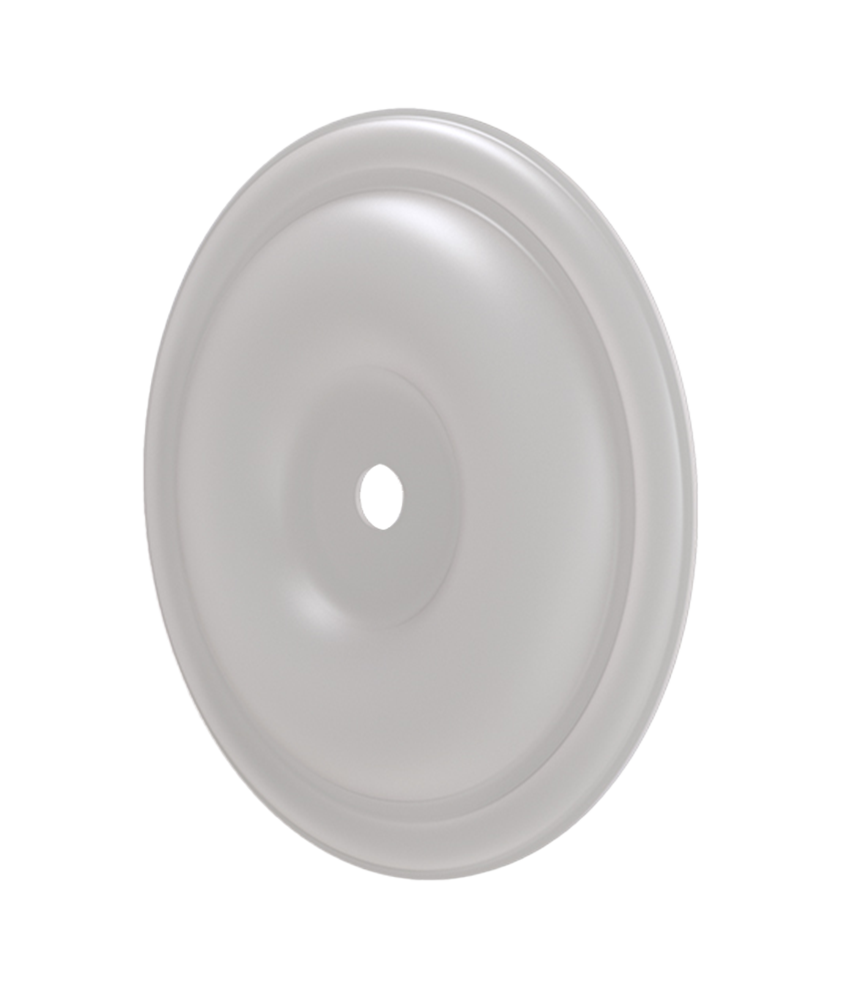
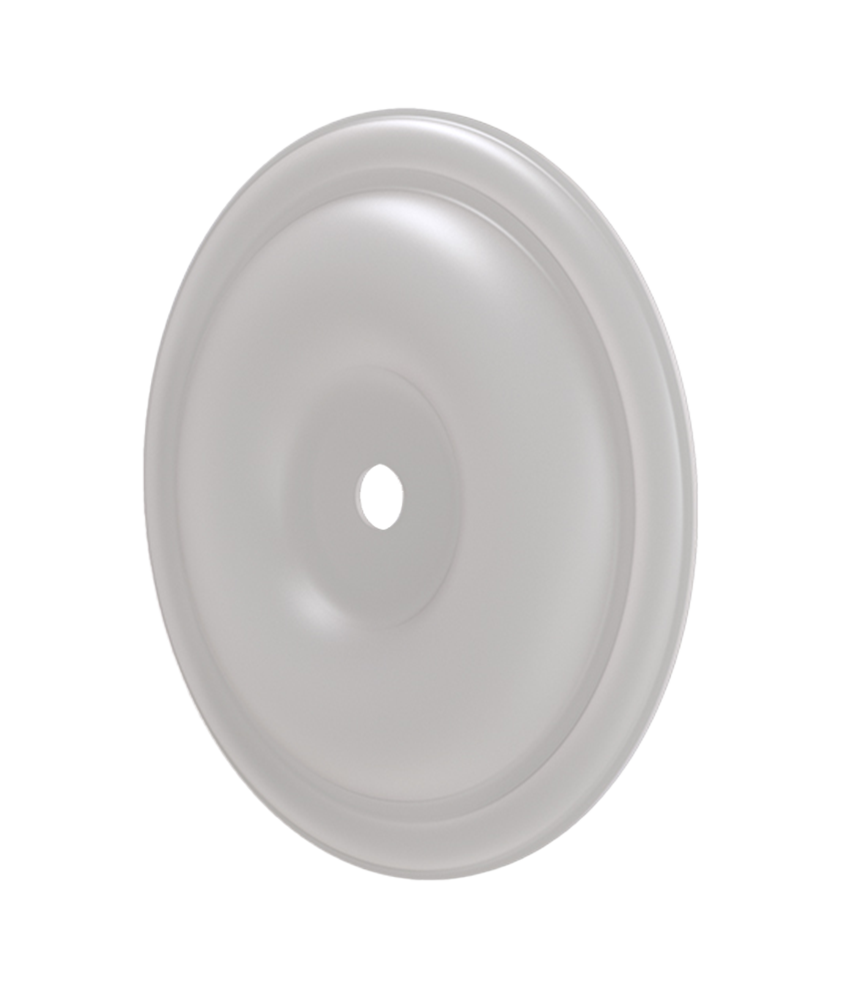
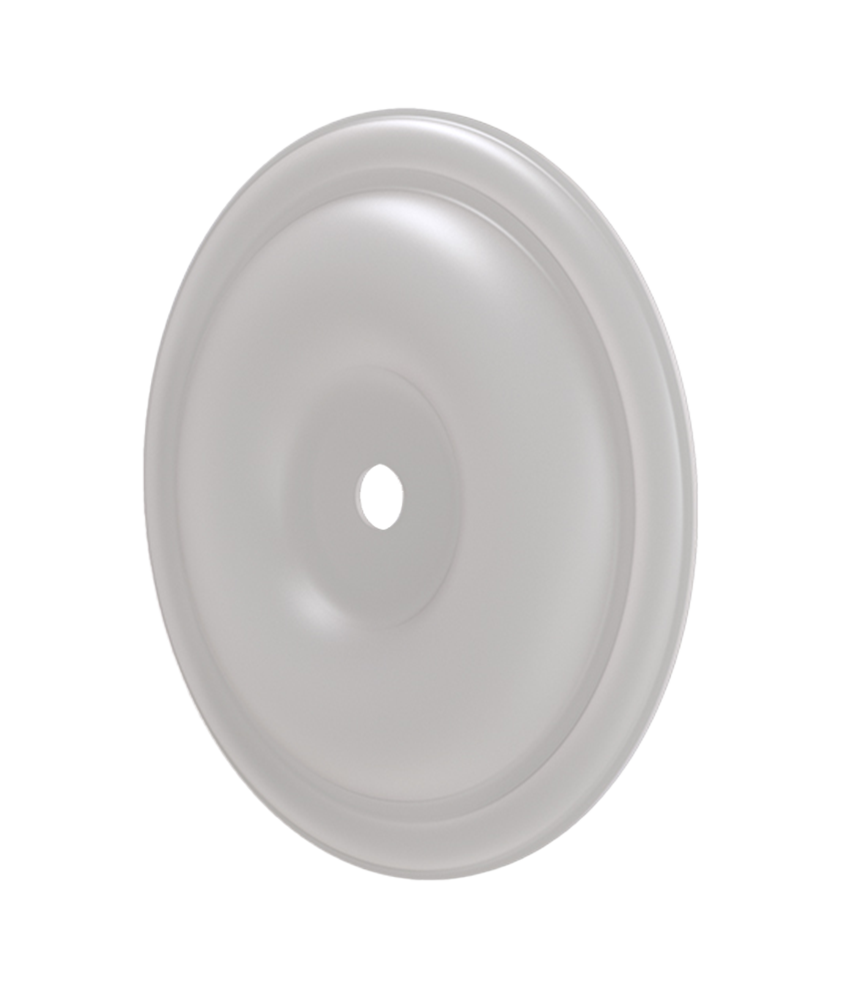
Diaphragms in Debem PTFE undergo a double heat treatment to increase their elasticity and service life. A sample of each batch is subject to destructive tests to check their compliance with the technical requirements. This diaphragm can be installed combined with one of the ones examined earlier (HYTREL® – SANTOPRENE®), in order to increase the resistance to the corrosive chemical agents and temperature of the fluid. PTFE is chemically inert and practically impenetrable. Not suitable for use with molten alkaline metals, abrasive liquids, suspended solids, chlorine or oxygen trifluoride or difluoride.
Rubber diaphragms
Debem’s rubber diaphragms offer high resistance and a unique mechanical bending capacity, thanks to the special additives in the rubber mixture that also improve the chemical characteristics.






They also have an internal nylon cloth reinforcement that improves stress distribution across the surface.
NBR: Inexpensive and particularly suited for petroleum-based liquids, aliphatic hydrocarbons, oil and abrasive fluids whilst on the other hand it is not suited for chlorinated solvents or acids.
EPDM: Good resistance to acids, alkaline and abrasion as well as a good flexibility also at low temperatures. Not suitable for oil and mineral greases.
Production test
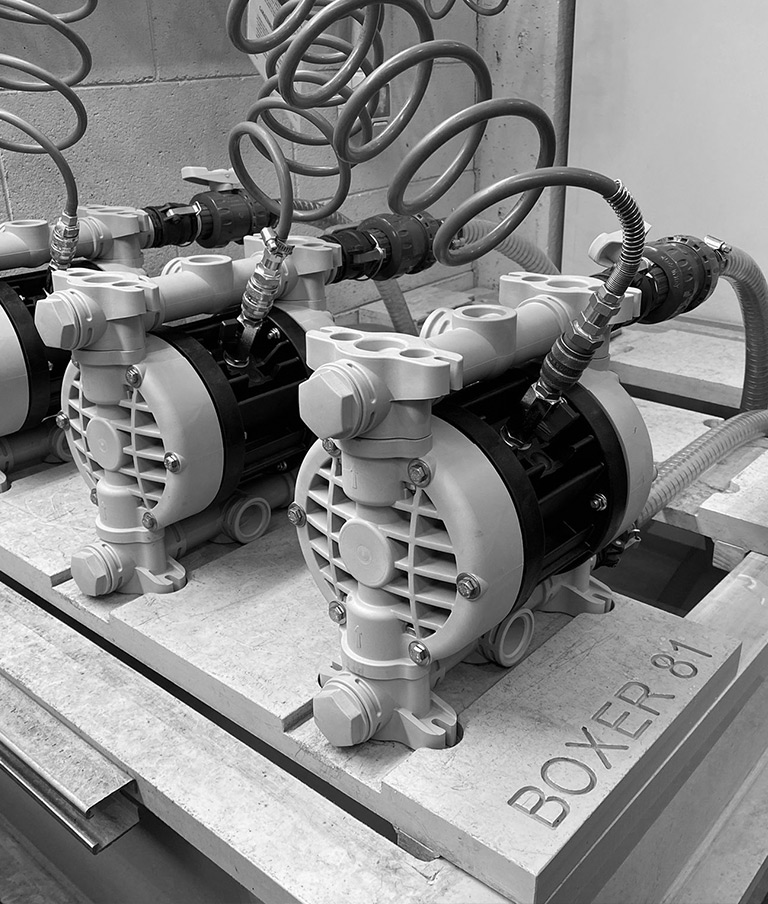
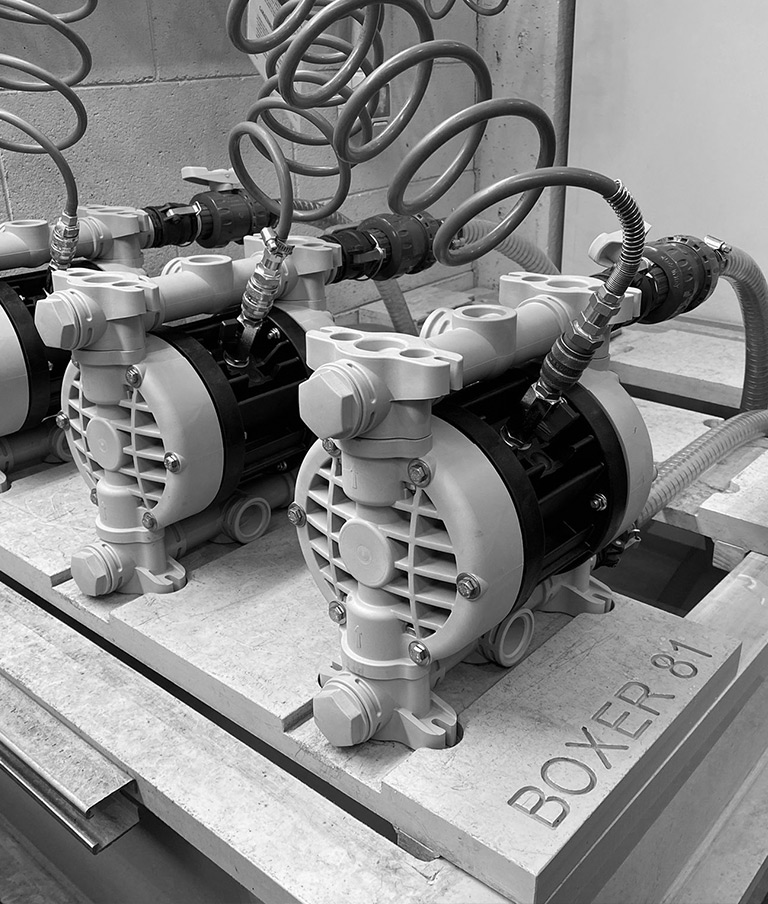
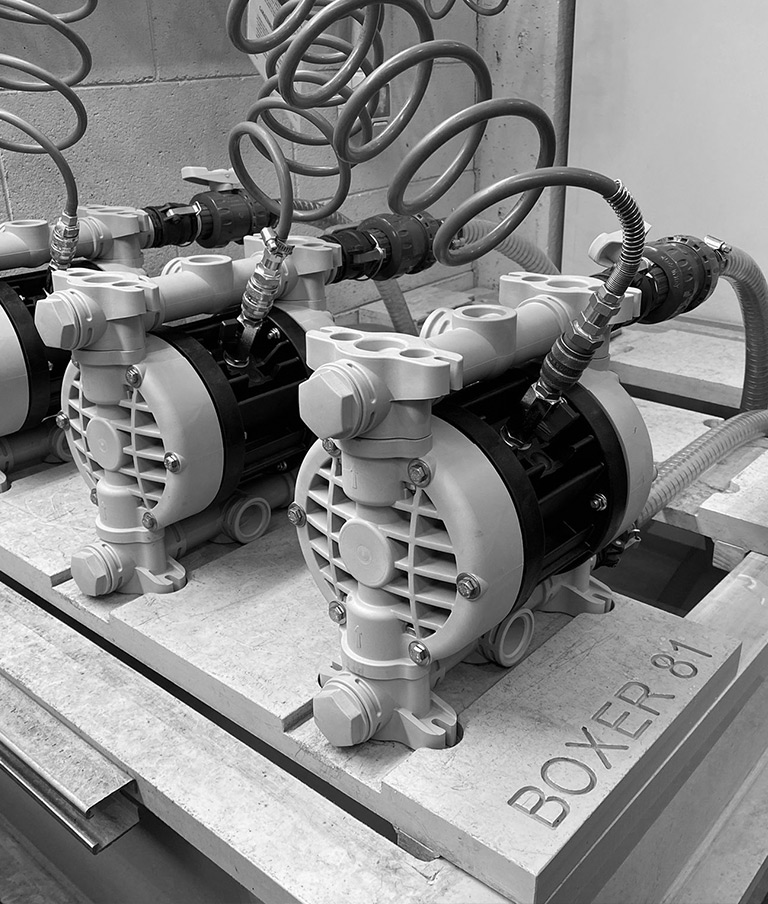
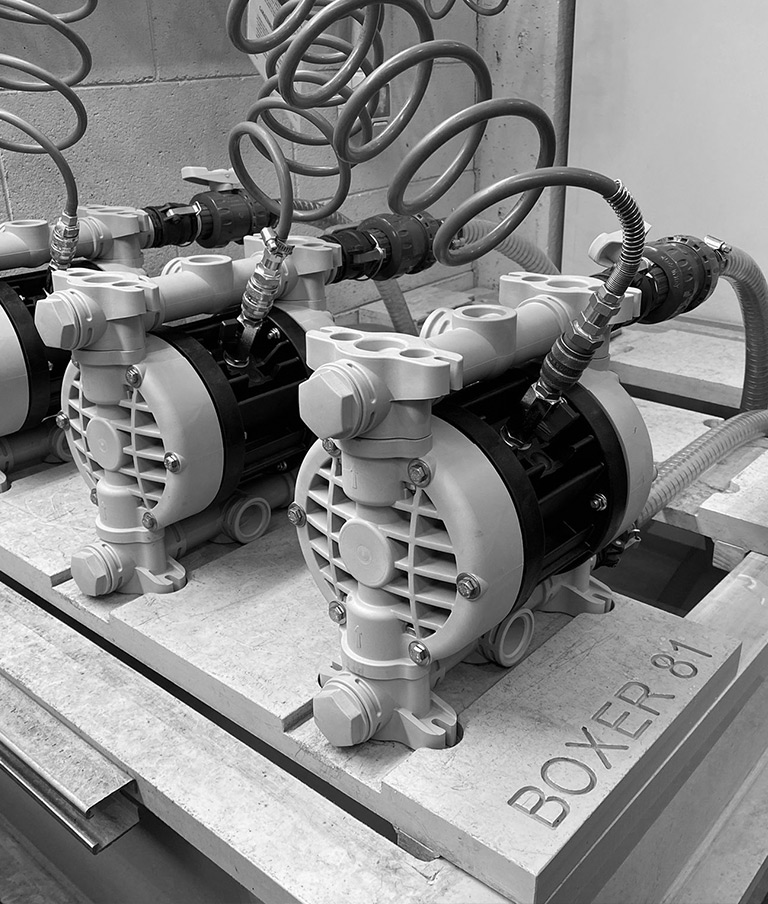
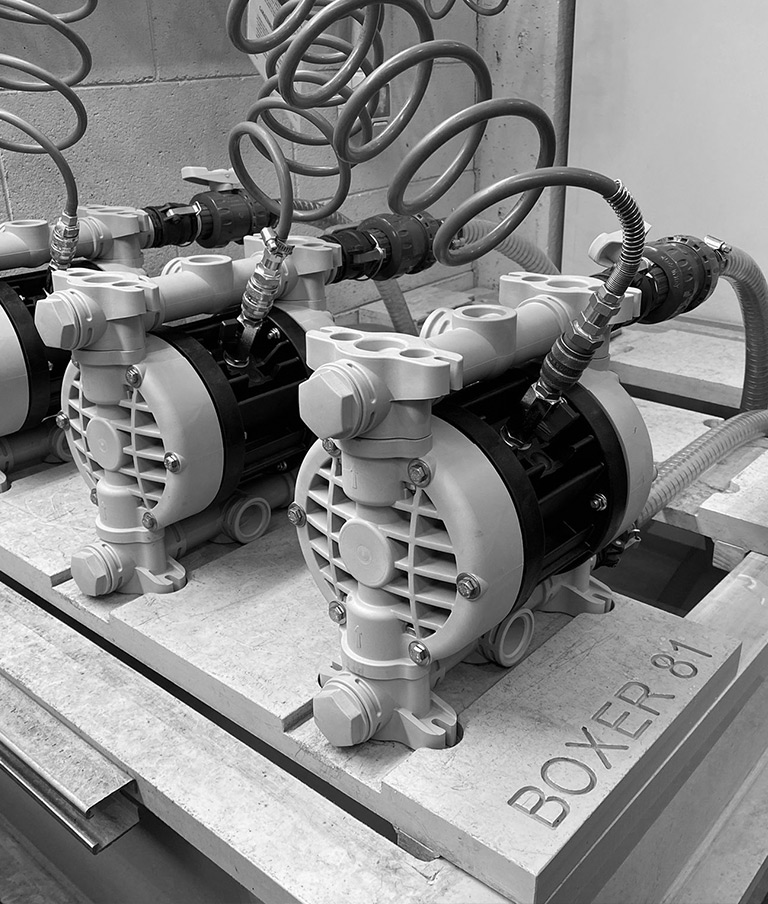
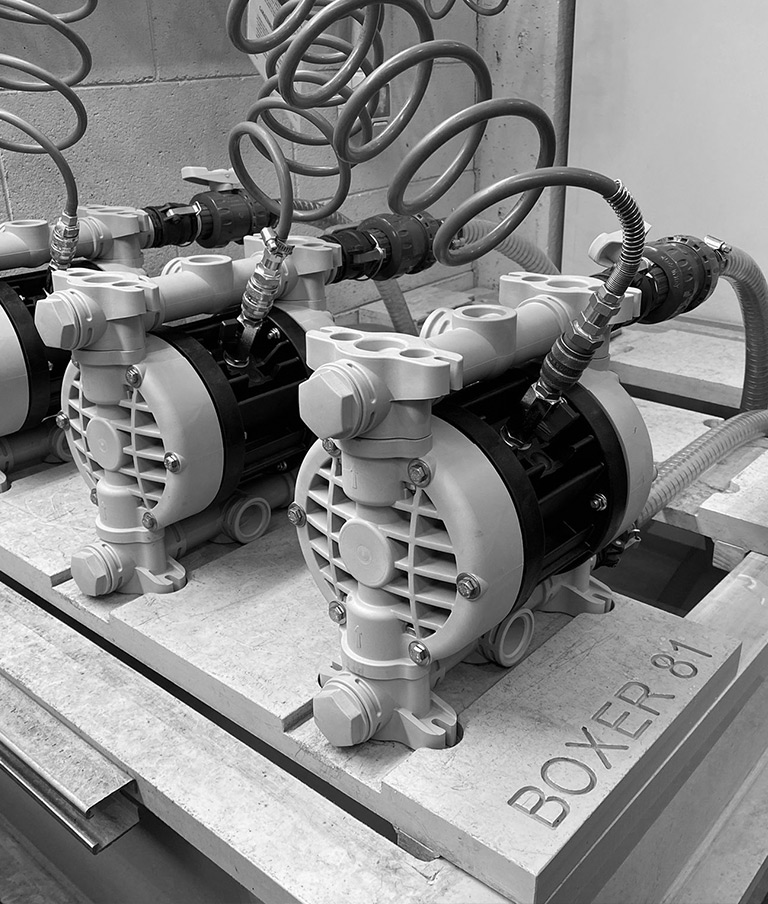
We test every pump (100% test), from the smallest (MIDGETBOX) to the largest, the BOXER 503. There are two distinct tests: the suction check and the correct product operation check, which also checks for any leaks. We don’t perform sample or batch tests.
Materials
Our plastics are reinforced with carbon fibers (to make them conductive) or glass fibers (to make them mechanically more performing). Our POLYPROPYLENE also undergoes a stabilization process in which all the details, once molded, are placed in an oven at 60 ° C for about 15 minutes and left to cool naturally.
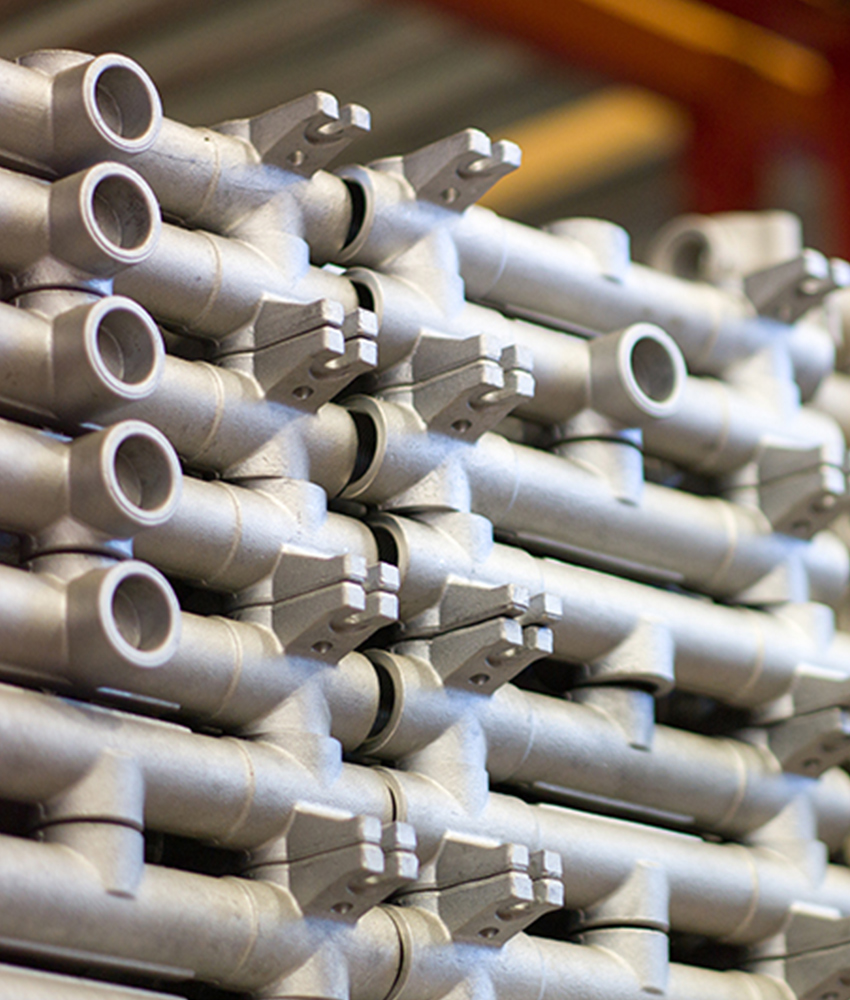
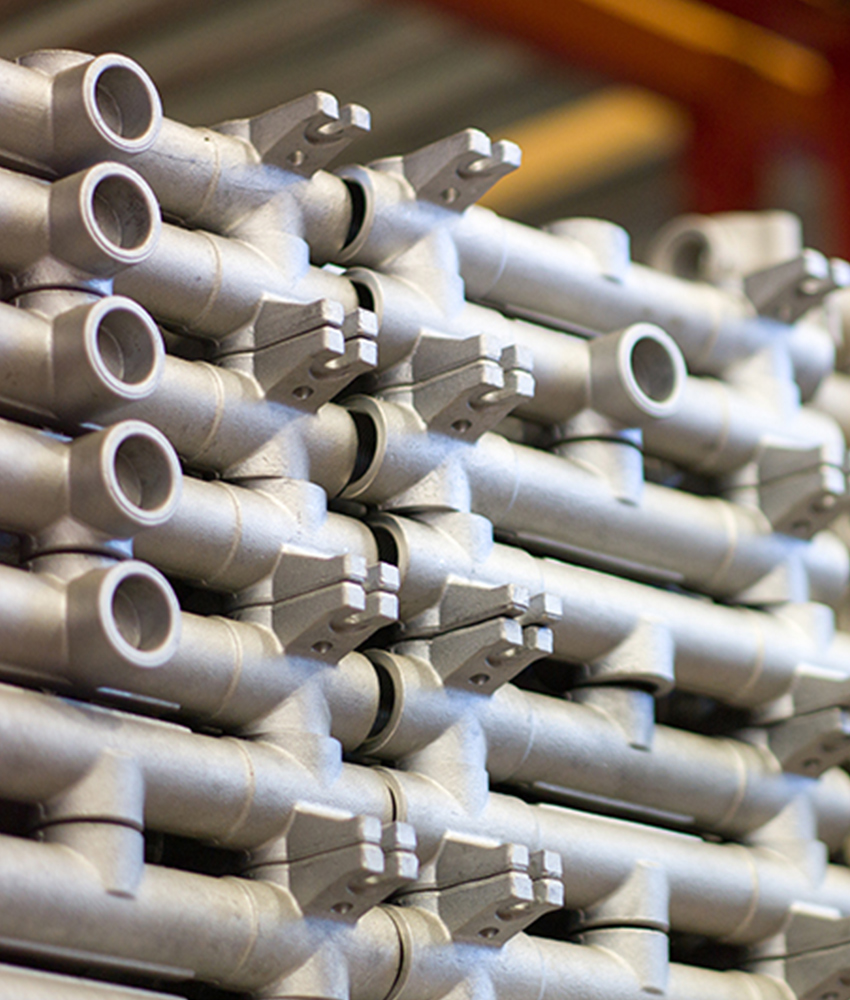
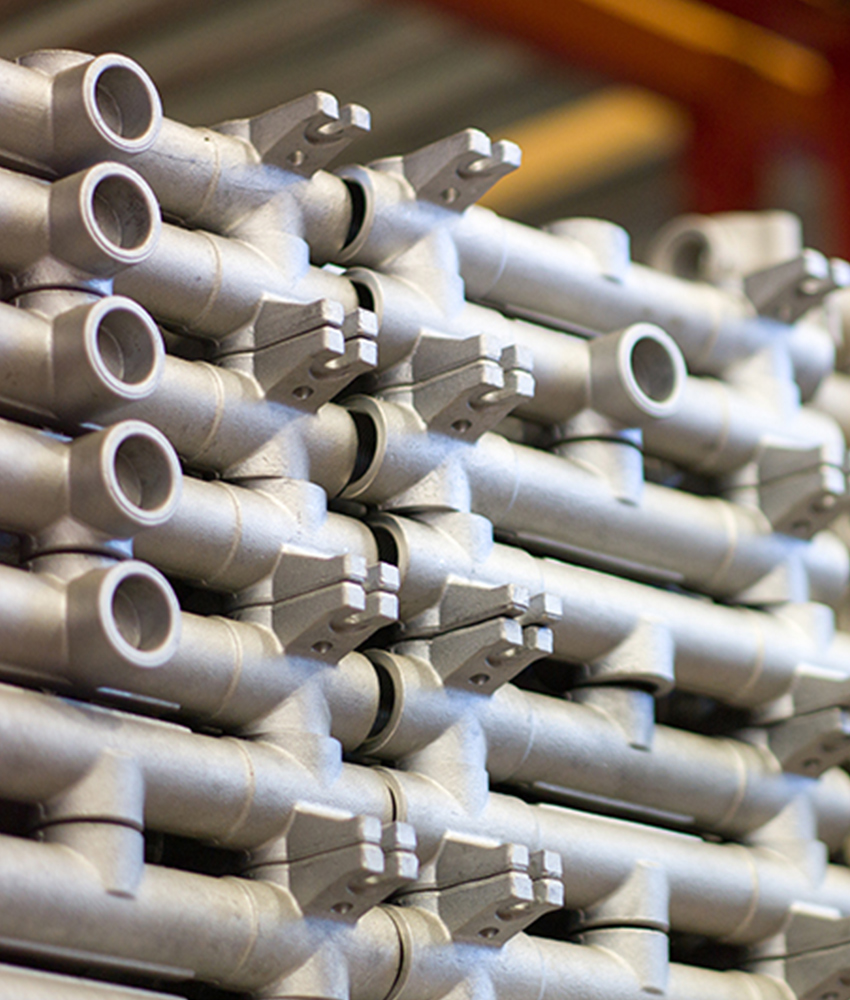
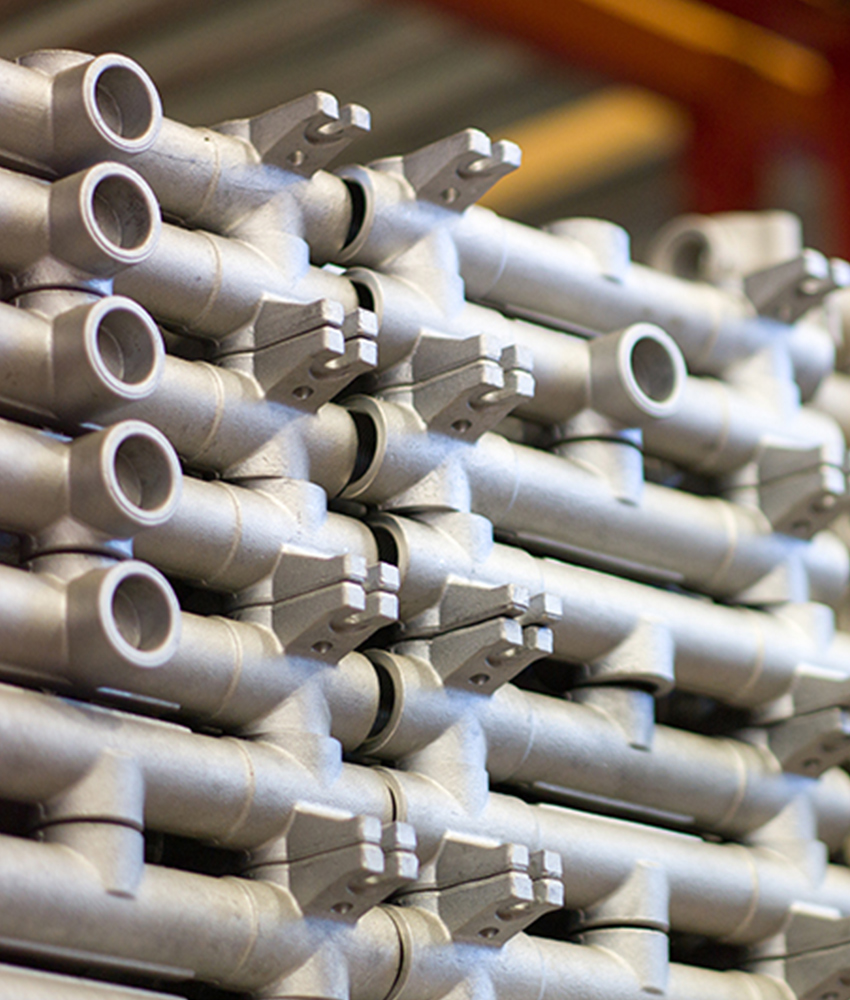
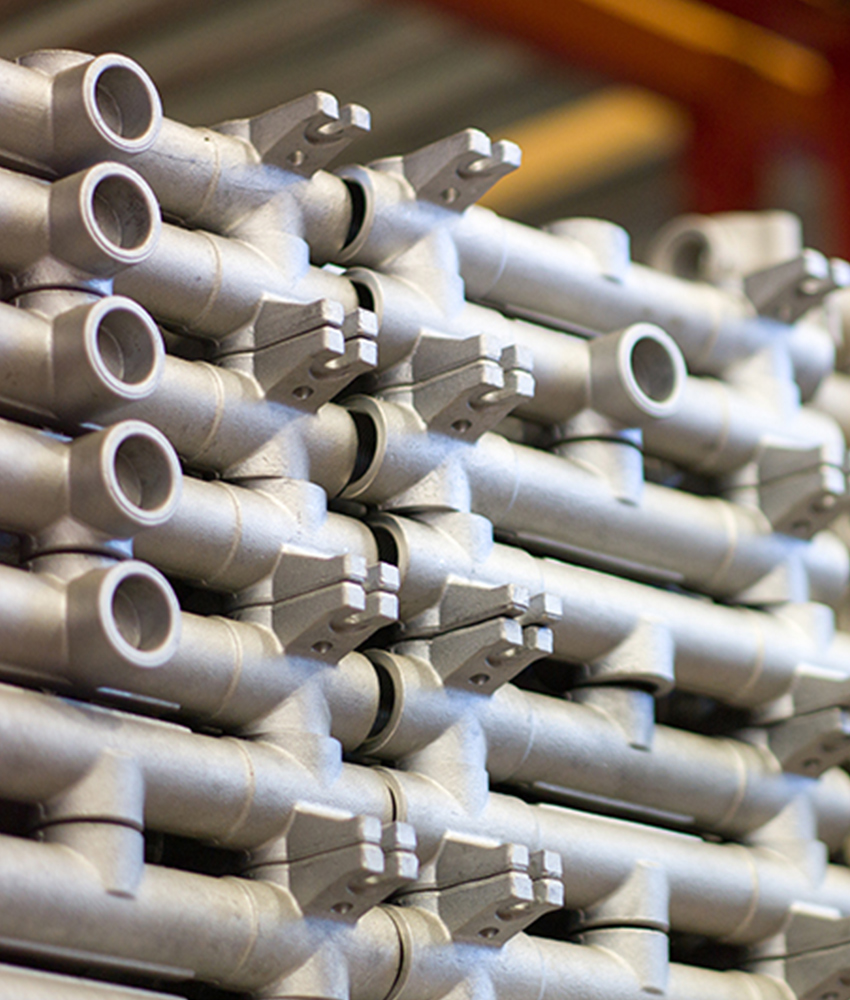
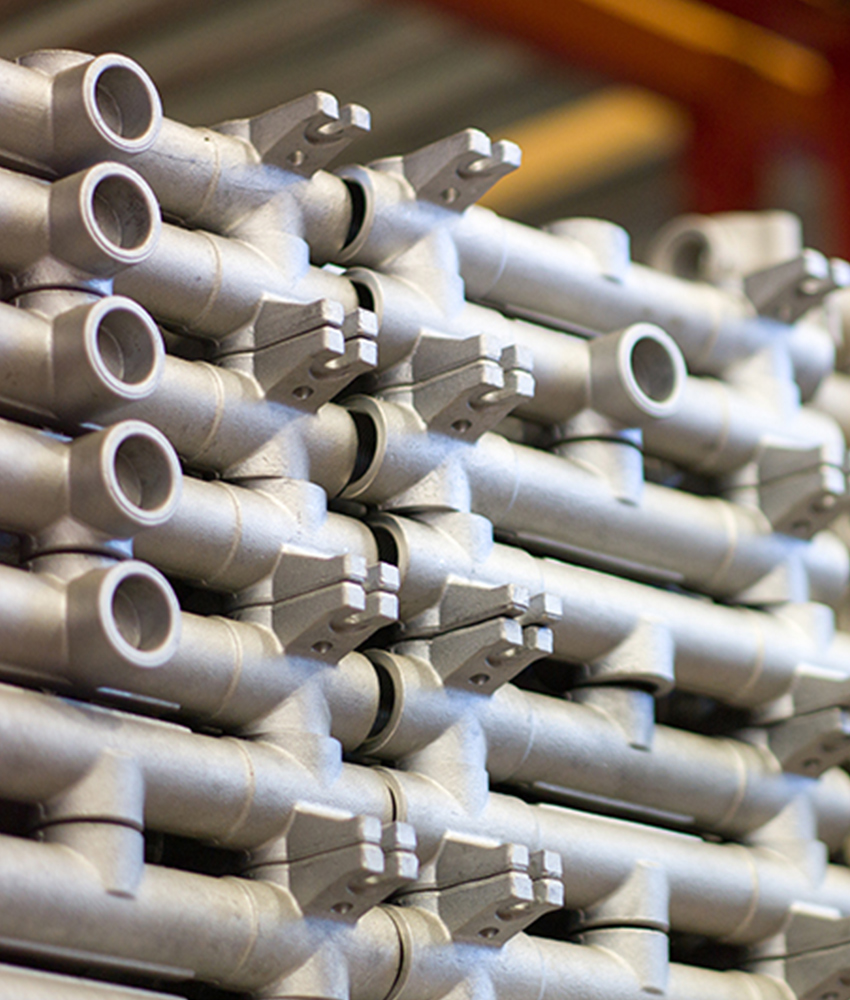
Our aluminium is obtained through a procedure called die casting, using a high-quality raw material, that is the same as the one used in the automotive industry. Our SS 316 s certified by our Italian supplier, with tests at the end of every production batch, that guarantee that only SS 316 is used to produce the parts. Our PTFE undergoes special treatments to render it more elastic and resistant to fatigue and wear. Elimination of the crystalline. Preforming the diaphragms – NO DEFORMING. Heat treatment similar to metal tempering, a continuous heating and cooling process that strengthens the molecular structure.